In today’s fast-paced manufacturing world, the use of robots for welding has become increasingly popular. Many companies are turning to robotic welding systems to improve their production processes. But why should you consider using a robot for your welding needs? This article will explore the many benefits of robotic welding and help you understand why it might be the right choice for your business.
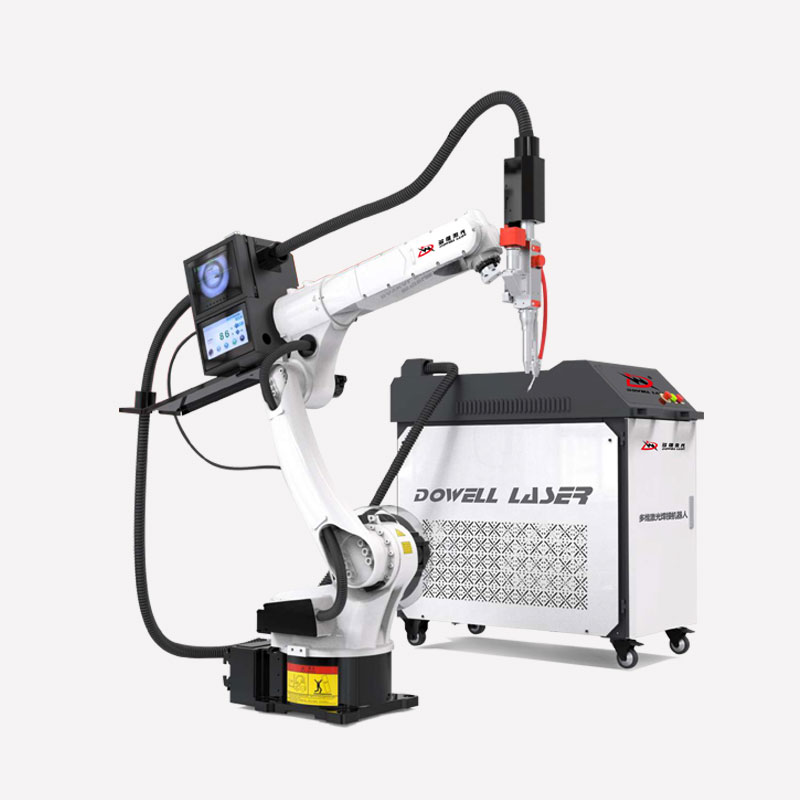
What is Robotic Welding?
Robotic welding is a technology that utilizes programmable robots to automate the welding process. These robots are equipped with advanced sensors, cameras, and software that enable them to perform precise and consistent welding tasks. Unlike manual welding, where human welders are responsible for manipulating the welding equipment, robotic welding involves the use of machines to carry out the welding operations.
Types of Robotic Welding
There are several types of robotic welding techniques, each suited to specific applications:
- Arc Welding Robot: This is one of the most common types of robotic welding. It uses an electric arc to melt and join metals. Arc welding is ideal for thick materials and is widely used in the automotive and construction industries.
- Spot Welding Robot: Typically used in the automotive industry, spot welding involves welding two or more metal sheets together at specific points. This type of welding is efficient for high-volume production lines.
- TIG Welding Robot: Tungsten Inert Gas (TIG) welding is known for its precision and is used for welding thin materials. It’s suitable for applications requiring high-quality welds, such as aerospace and electronics manufacturing.
- MIG Welding Robot : Metal Inert Gas (MIG) welding is versatile and can be used for a wide range of materials. It’s commonly used in fabrication and repair shops.
- Laser Welding Robot: This high-speed welding process uses laser beams to join metals. It’s perfect for applications that require minimal heat input and high accuracy.
Components of a Robotic Welding System
- Robotic Arm: The arm is the primary tool that moves and manipulates the welding torch. It can be programmed to move with precision and repeatability.
- Welding Torch: This component is responsible for delivering the welding current and heat to the workpiece.
- Controller: The controller is the brain of the robotic system. It processes the instructions and commands the robot’s movements.
- Sensors and Cameras: These devices provide feedback to the robot, ensuring it can adapt to variations in the welding environment.
- Safety Enclosures: To protect workers and ensure safe operation, robotic welding systems are often enclosed within safety barriers.
Robotic Laser Welding Advantages:
Improved Precision and Consistency
One of the most significant advantages of robotic welding is the level of precision and consistency it offers. Unlike human welders, who may experience fatigue and inconsistency over long periods, robots can perform the same welding task repeatedly without deviation. This precision ensures high-quality welds, reducing the likelihood of defects and rework.
Repeatability: Robots can execute the same welding task with exactness, ensuring that each weld is consistent across the production line.
Accuracy: Advanced sensors and control systems allow robots to adjust to variations in the welding process, maintaining a high level of accuracy.
Enhanced Productivity and Efficiency
Robotic welding systems significantly enhance productivity by reducing cycle times and increasing throughput. Robots can work continuously without breaks, maximizing uptime and output. This efficiency translates to cost savings and faster project completion times.
Speed: Robots can operate at higher speeds than human welders, completing tasks in less time.
24/7 Operation: Robotic systems can run continuously, enabling around-the-clock production and reducing downtime.
Improved Safety
Welding can be hazardous, involving exposure to high temperatures, fumes, and ultraviolet radiation. Robotic welding minimizes these risks by removing human operators from the direct welding environment. This leads to a safer workplace and reduces the risk of injuries.
Risk Reduction: By automating the welding process, robots eliminate the need for human welders to be exposed to dangerous conditions.
Hazardous Material Handling: Robots can handle materials that may be too dangerous for humans, further enhancing safety.
Cost-Effectiveness
While the initial investment in robotic welding systems can be significant, the long-term cost savings are substantial. Reduced labor costs, increased productivity, and lower defect rates contribute to a higher return on investment (ROI).
Reduced Labor Costs: Robots can perform tasks that would otherwise require multiple human workers, lowering labor expenses.
Lower Scrap Rates: The precision of robotic welding reduces waste and rework, saving material costs.
Flexibility and Adaptability
Modern robotic welding systems are highly adaptable, capable of handling various welding tasks and materials. They can be reprogrammed for new projects, making them a versatile solution for manufacturers facing changing production demands.
Multi-Tasking: Robots can be equipped to perform multiple types of welding, allowing manufacturers to switch between tasks seamlessly.
Adaptability: As production needs change, robots can be reprogrammed to accommodate new welding requirements.
How Robotic Welding Improves Efficiency
Increased speed and productivity:
Robotic welders can work continuously without breaks or fatigue, allowing for 24/7 operation if needed.
Robots can achieve up to 85% efficiency, compared to around 20% for human welders.
The consistent speed and cycle times of robots lead to higher throughput and production rates.
Consistent quality:
Robots maintain precise welding parameters like speed, current, and torch angle throughout the entire process.
This consistency results in uniform, high-quality welds that require less rework or rejection.
Reduced waste and costs:
Precise control means less wasted welding materials, gas, and other consumables.
Fewer errors and rejected parts lead to cost savings.
Lower labor costs as robots can work longer hours without overtime pay.
Improved scheduling and throughput:
Predictable cycle times make production scheduling easier and help eliminate bottlenecks.
Consistent throughput helps manufacturers deliver components on time.
Less post-weld cleanup:
Robots weld cleanly and precisely, reducing the need for post-weld cleanup and dressing.
Flexibility for different tasks:
Modern robots can be quickly reprogrammed for different welding jobs, allowing for efficient handling of various products or small batch runs.
Addressing skills shortages:
Robots can take on routine welding tasks, allowing skilled human welders to focus on more complex jobs.
Robotic Welding Applications
Automotive Industry
Spot welding: widely used for joining sheet metal parts in automotive manufacturing.
Arc welding: used for structural welding of automotive frames and parts.
Aerospace Industry
TIG welding: used for welding thin materials in aircraft manufacturing, ensuring high-strength joints.
Laser welding: used for precisely joining complex aerospace components.
Construction and Infrastructure
MIG welding: used for manufacturing structural steel components.
Arc welding: used for welding large diameter pipes and beams.
Electronics and Consumer Goods
Micro welding: used for delicate welding tasks in electronics assembly.
Resistance welding: used for joining small components in consumer goods.
Shipbuilding and Marine Industry
Heavy Duty Welding: used for welding thick plates in ship construction.
Spot welding: used for high-precision assembly of ship components.
When to Consider Industrial Robotic Welding
- High-Volume Production: Robotic welding is particularly well-suited for high-volume production runs where consistency and efficiency are paramount.
- Complex Welding Tasks: If your welding tasks involve complex geometries, tight tolerances, or hazardous materials, robotic welding can provide a safer and more reliable solution.
- Repetitive Tasks: Robotic welding can automate repetitive tasks, freeing up human workers to focus on more complex and value-added activities.
Conclusion
Robotic welding offers a compelling solution for manufacturers seeking to improve the quality, efficiency, and safety of their welding operations. By leveraging the precision, speed, and flexibility of robotic systems, businesses can gain a competitive edge in today’s demanding market.
While the decision to invest in robotic welding should be carefully evaluated based on specific production requirements, the benefits are clear: enhanced precision, increased productivity, improved safety, and long-term cost-effectiveness.