In the rapidly evolving world of manufacturing, precision and efficiency are paramount. Laser profile cutting machines have become an essential tool in achieving these goals. But what exactly is a laser profile cutting machine, and why is it so important in modern manufacturing? This comprehensive guide will answer these questions and more, providing a detailed look into the world of laser profile cutting.

How Laser Profile Cutting Works
Laser profile cutting involves using a high-powered laser beam to cut precise shapes and profiles from various materials. The laser beam is directed by computer numerical control (CNC) systems, which ensure accuracy and repeatability. The process involves focusing the laser to a fine point, which melts, burns, or vaporizes the material along a predefined path.
Types of Lasers Used in Profile Cutting
There are several types of lasers used in profile cutting, including CO2 lasers, fiber lasers, and Ndlasers. Each type has its own advantages:
- CO2 Lasers: Ideal for cutting non-metal materials such as wood, plastic, and glass.
- Fiber Lasers: Excellent for cutting metals due to their high power and efficiency.
- NdLasers: Used for applications requiring high peak power, such as welding and engraving.
Advantages of Laser Profile Cutting Machines
Precision and Accuracy
One of the primary benefits of laser profile cutting is its exceptional precision. The focused laser beam can achieve extremely fine cuts, making it ideal for intricate designs and detailed work.
Speed and Efficiency
Laser profile cutting machines operate at high speeds, significantly reducing production time. This efficiency is particularly beneficial for large-scale manufacturing projects.
Versatility in Material Handling
These machines can cut a wide range of materials, from metals and plastics to wood and ceramics. This versatility makes them suitable for various industries and applications.
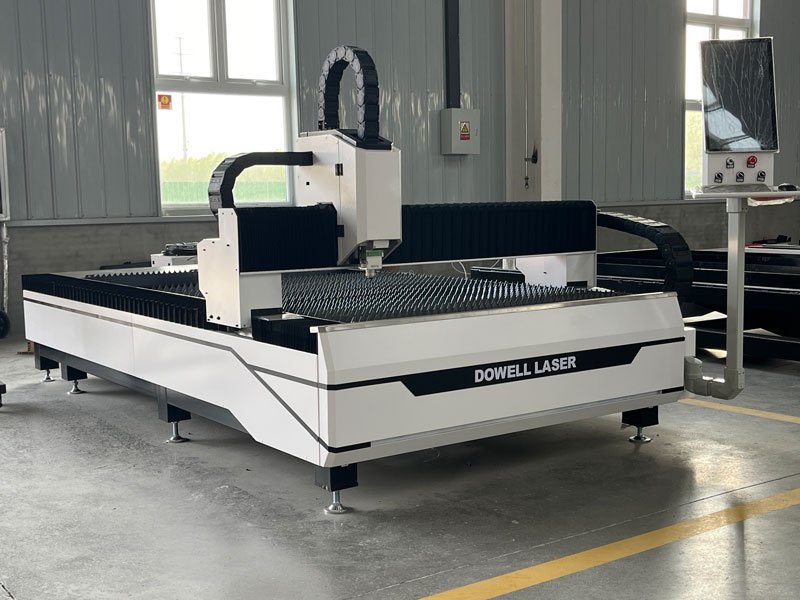
Applications of Laser Profile Cutting Machines
Automotive Industry
Laser profile cutting is widely used in the automotive industry for cutting complex shapes and components with high precision. This technology helps in manufacturing lightweight and strong parts, enhancing vehicle performance and safety.
Aerospace Industry
In the aerospace sector, precision and accuracy are critical. Laser profile cutting machines are used to fabricate components that meet stringent quality standards, ensuring the reliability and safety of aircraft.
Construction and Architecture
For construction and architectural applications, laser profile cutting machines offer the ability to create detailed designs and custom components. This technology is used in the production of structural elements, decorative pieces, and more.
Custom Fabrication
Custom fabrication businesses benefit from the flexibility of laser profile cutting. They can produce unique, high-quality products tailored to specific customer requirements, ranging from artwork to industrial parts.

Choosing the Right Laser Profile Cutting Machine
Key Factors to Consider
When selecting a laser profile cutting machine, consider the following factors:
- Material Types: Ensure the machine can handle the materials you plan to cut.
- Cutting Speed: Look for a machine that offers the required speed for your production needs.
- Precision and Accuracy: Choose a machine that meets your precision requirements.
- Size and Power: Consider the size of the machine and its power output to ensure it fits your workspace and production demands.
Comparing Different Models
Research and compare different models based on their features, capabilities, and customer reviews. Consider reaching out to manufacturers for demonstrations and additional information.
Cost Considerations
While price is a significant factor, it’s important to balance cost with the machine’s capabilities and long-term value. Investing in a higher-quality machine may result in better performance and durability.
Setting Up a Laser Profile Cutting Machine
Installation Requirements
Proper installation is crucial for optimal performance. Ensure you have adequate space, ventilation, and power supply. Follow the manufacturer‘s guidelines for setting up the machine.
Safety Precautions
Safety should be a top priority. Equip your workspace with appropriate safety gear, such as laser safety glasses and protective barriers. Train operators on safe handling and emergency procedures.
Initial Calibration
Calibrate the machine according to the manufacturer’s instructions to ensure accurate cuts. Regular calibration checks are essential for maintaining precision over time.
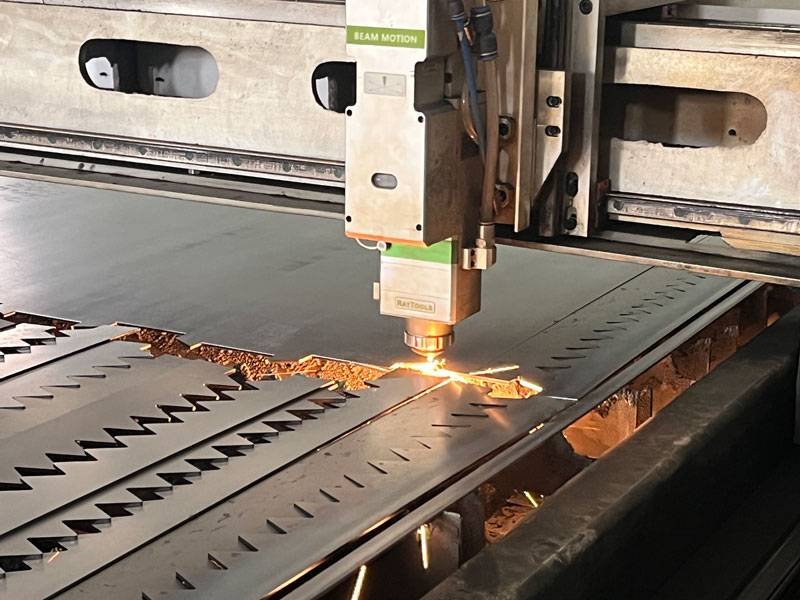
Operating a Laser Profile Cutting Machine
Basic Operation Steps
- Power On: Start by powering on the machine and ensuring all systems are functional.
- Load Material: Secure the material to be cut on the machine’s worktable.
- Set Parameters: Input the necessary cutting parameters, such as laser power, speed, and focus.
- Begin Cutting: Start the cutting process, monitoring for any issues.
Software and Programming
Familiarize yourself with the machine’s software for designing and programming cuts. Understanding how to create and modify cutting paths will improve efficiency and precision.
Common Operational Challenges
Operators may encounter challenges such as material warping, inconsistent cuts, or machine malfunctions. Troubleshooting guides and manufacturer support can help address these issues.
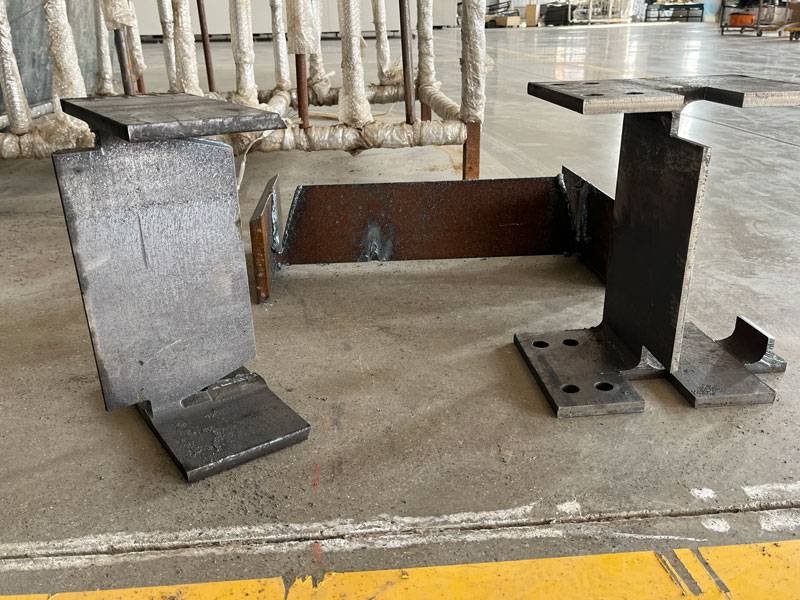
Maintenance and Troubleshooting
Regular Maintenance Tasks
- Cleaning: Regularly clean the machine’s lenses, mirrors, and worktable.
- Inspection: Check for wear and tear on moving parts and replace them as needed.
- Alignment: Ensure the laser beam is properly aligned for accurate cutting.
Common Issues and Solutions
Common issues include poor cut quality, laser power fluctuations, and software errors. Routine maintenance and prompt troubleshooting can minimize downtime and extend the machine’s lifespan.
Extending Machine Lifespan
Proper maintenance, regular calibration, and following the manufacturer‘s guidelines can significantly extend the lifespan of your laser profile cutting machine, ensuring consistent performance and reliability.
Future Trends in Laser Profile Cutting Technology
Technological Innovations
Advancements in laser technology, such as higher power outputs and improved beam quality, are making laser profile cutting machines more capable and versatile.
Industry Developments
The integration of AI and machine learning in laser profile cutting machines is enhancing automation and precision. These technologies enable real-time adjustments and predictive maintenance, further improving efficiency.
The Role of Automation
Automation is playing an increasingly significant role in laser profile cutting. Automated systems can handle material loading, cutting, and sorting, reducing the need for manual intervention and increasing production speed.
Conclusion
Laser profile cutting machines are transforming the manufacturing landscape with their precision, speed, and versatility. Understanding how to choose, operate, and maintain these machines is crucial for maximizing their benefits. As technology continues to advance, the future of laser profile cutting looks promising, with innovations driving further improvements in efficiency and capabilities.
FAQs
What materials can be cut with a laser profile cutting machine?
Laser profile cutting machines can cut a wide range of materials, including metals (such as steel, aluminum, and brass), plastics, wood, ceramics, and composites.
How does laser profile cutting compare to other cutting methods?
Laser profile cutting offers superior precision, speed, and flexibility compared to traditional cutting methods such as mechanical sawing or plasma cutting. It also produces cleaner cuts with minimal material waste.