This article will mainly focus on the laser welding problem solution to explain the laser welding problem, I hope it can be helpful to you.
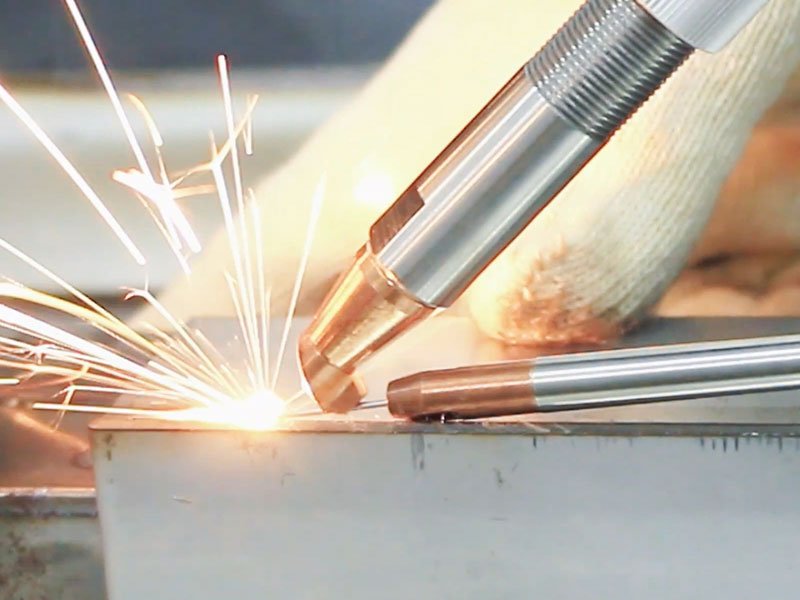
Laser welding advantages and disadvantages
Advantages of laser welding
High Precision and Quality
- Narrow Heat-Affected Zone: Laser welding produces a very narrow heat-affected zone compared to traditional welding methods. This minimizes distortion and damage to the surrounding material, resulting in a more precise weld.
- High Welding Speed: It can complete welding operations at a relatively high speed. This is particularly beneficial in mass production environments where efficiency is crucial.
- Excellent Weld Appearance: The welds created by laser welding are often smooth and aesthetically pleasing, with minimal spatter and consistent bead formation.
Versatility
- Wide Range of Materials: Laser welding can be used on a variety of materials including metals such as steel, aluminum, titanium, and alloys. It can also be applied to dissimilar materials, enabling unique manufacturing possibilities.
- Complex Geometries: It is capable of welding complex shapes and geometries, including parts with thin walls or hard-to-reach areas. This makes it suitable for intricate designs in industries like aerospace and electronics.
Automation Compatibility
- Easy Integration with Robots: Laser welding systems can be easily integrated with robotic arms for automated welding processes. This allows for consistent and repeatable welds, reduces labor costs, and improves production throughput.
- Programmable: The welding parameters can be programmed precisely, enabling the welding of different parts with minimal setup time changes.
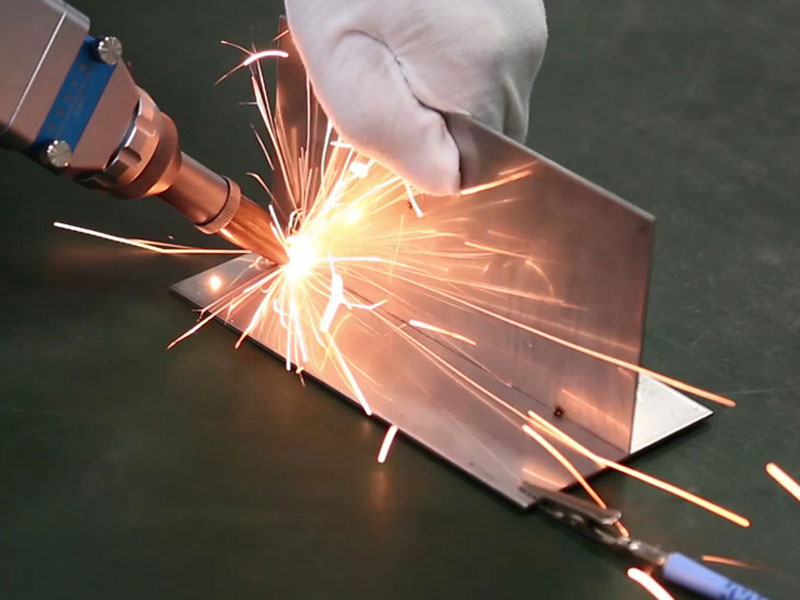
Disadvantages of laser welding
High Equipment Cost
- Initial Investment: The cost of purchasing a laser welding machine is relatively high. This includes not only the laser source but also the associated optics, cooling systems, and control units. This high upfront cost can be a barrier for small and medium-sized enterprises.
- Maintenance Expenses: The maintenance of laser welding equipment requires specialized knowledge and can be expensive. Components such as laser tubes or diodes may need to be replaced periodically, adding to the overall cost of ownership.
Limited Penetration Depth for Some Applications
- Thick Materials Challenges: While laser welding is effective for thin to moderately thick materials, there are limitations when it comes to very thick materials. Achieving deep penetration in thick materials may require extremely high laser power or multiple passes, which can be time-consuming and may affect the quality of the weld.
- Reflective Materials: Some highly reflective materials like copper can pose difficulties as they reflect a significant portion of the laser energy. This can lead to inconsistent welds or require additional measures such as surface treatment to enhance absorption.
Safety Concerns
- Laser Hazards: The laser beam used in welding is a potential hazard to human eyes and skin. Special safety precautions such as wearing appropriate protective eyewear and ensuring proper shielding of the work area are essential.
- Fumes and Particulates: The welding process generates fumes and particulates that can be harmful if not properly ventilated. This requires the installation of adequate ventilation systems to protect the health of workers.
Common laser welding problems
1.Welding cracks
Causes of hot cracks:
- Cooling too fast is a key factor that causes hot cracks. When the weld area cools quickly, the solidification process in the weld metal is uneven, which is prone to thermal stress. When the thermal stress exceeds the strength limit of the material, hot cracks will form.
- Material composition also plays an important role. Excessive or low content of certain alloying elements may change the crystallization characteristics of the weld metal, making it more susceptible to hot cracks. For example, impurity elements such as sulfur and phosphorus will reduce the crack resistance of the weld metal.
Causes of cold cracks:
- Hydrogen is one of the main factors that cause cold cracks. During welding, hydrogen atoms may dissolve in the weld metal. During cooling, hydrogen atoms will gather at microscopic defects inside the metal to form hydrogen molecules, generating huge internal stress, thereby causing cold cracks.
- When the constraint of the weld joint is large, the constraint stress of the weld metal during cooling and shrinkage will also increase, which is easy to cause cold cracks.

2.Porosity formation
Problems related to shielding gas lead to pores:
- One of the common reasons is that the flow rate of shielding gas is not suitable. If the flow rate is too small, the air around the welding area cannot be effectively removed, and the oxygen, nitrogen, etc. in the air will enter the molten pool, forming pores during the solidification of the weld metal.
- Insufficient purity of shielding gas can also cause problems. Impurity gases may react with the molten pool metal to generate gas products and form pores.
Situations where material impurities cause pores:
Some volatile impurities contained in the material itself, such as moisture, oil, etc., will decompose and produce gas at high welding temperatures. If these gases cannot escape from the molten pool in time, pores will form in the weld.
3.Weld shape defects
Factors affecting uneven weld width:
Unstable laser welding power can cause changes in weld width. Power fluctuations may be caused by unstable laser sources or fluctuations in power supply.
Uneven welding speed is also an important factor. For example, if the speed of a welding robot changes during movement, the heat input to the weld will be uneven, resulting in inconsistent weld width.
Causes of weld undercut:
Improper welding parameter settings are one of the main reasons. If the welding current is too large or the welding speed is too fast, the metal liquid in the molten pool will not have time to fill the edge of the weld, resulting in undercutting.
Welding operation techniques can also have an impact. During manual welding, the welder’s lack of operating skills and experience may result in inappropriate angles and positions of the welding gun, resulting in undercutting.
4.Insufficient welding strength
The influence of welding process parameters on strength:
- Welding power that is too low will lead to insufficient penetration of weld metal and insufficient bonding between the weld and the base material, thereby reducing welding strength.
- Welding speed that is too fast will coarsen the crystal structure of the weld metal and reduce the mechanical properties of the weld.
Relationship between material matching and strength:
When the chemical composition, mechanical properties, etc. of the welding material and the base material do not match, the weld is prone to cracking or insufficient strength during use. For example, when welding dissimilar materials, if the appropriate filler material is not selected, the welding strength may not meet the requirements.
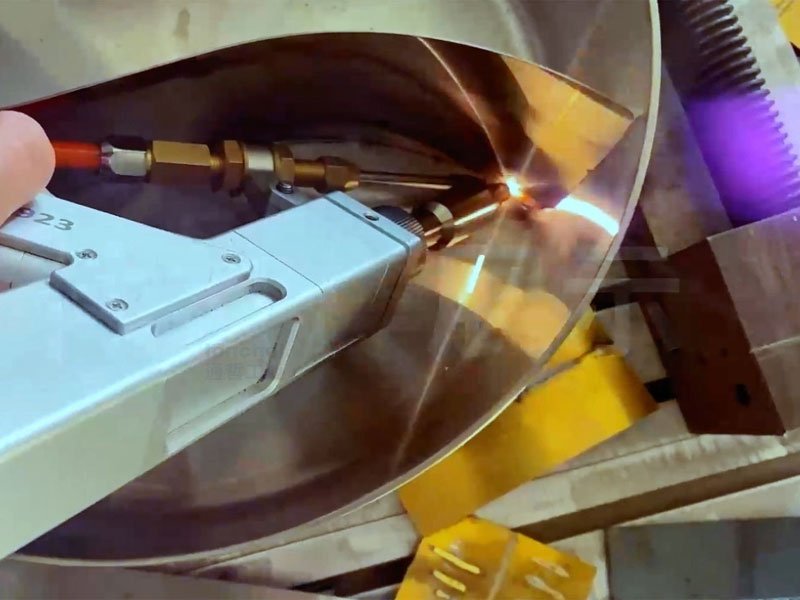
Detection methods for laser welding problems
1.Nondestructive testing technology
Application of ultrasonic testing in discovering internal defects:
- Ultrasonic testing is a method of detecting internal defects of welds by using the propagation characteristics of ultrasonic waves in materials. When ultrasonic waves encounter defects, reflection and refraction will occur. By receiving and analyzing these reflected waves, the location, size and shape of the defects can be determined.
- This detection method is suitable for detecting internal defects such as cracks, pores, slag inclusions in welds, and can quickly detect welds over a large area.
Principle and usage scenarios of radiographic testing:
- Radiographic testing uses X-rays or γ-rays to penetrate welds, and forms images of different blackness on photosensitive films according to the different absorption degrees of radiation in different parts of the weld, thereby detecting defects in welds.
- It is suitable for detecting volume defects inside welds, such as pores, slag inclusions, etc., but the detection sensitivity for planar defects such as cracks is relatively low. At the same time, radiographic testing needs to pay attention to radiation protection issues.
2.Key points of appearance inspection
Key points of visual observation of weld appearance:
- Check whether the surface of the weld is smooth and flat, and whether there are obvious defects such as cracks, pores, slag inclusions, etc.
- Observe whether the shape of the weld meets the requirements, including the width and uniformity of the weld.
Inspection method with tools such as magnifying glasses:
- Using a magnifying glass can more clearly observe the subtle defects on the weld surface, such as tiny pores, cracks, etc.
- For some welded parts with higher requirements, a microscope can be used for inspection to ensure the quality of the weld.
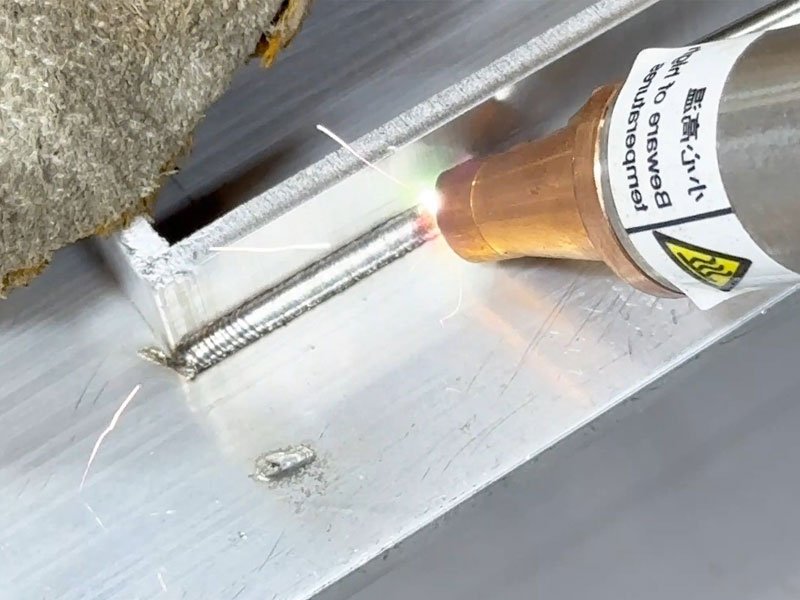
Solving laser welding problems
1.Optimizing welding process parameters
Power adjustment:
According to the thickness and type of the material, the power of laser welding should be reasonably adjusted. For thicker materials, higher power is required to ensure sufficient penetration depth; for thin materials, the power should be appropriately reduced to avoid over-welding.
During the welding process, the quality of the weld can be monitored in real time, and the power can be fine-tuned according to the actual situation to obtain the best welding effect.
Welding speed control:
It is crucial to maintain the uniformity of the welding speed. The stability of the welding speed can be ensured by optimizing the control system of the welding equipment, such as the motion control system of the welding robot.
According to the requirements of the welding process and the characteristics of the material, select the appropriate welding speed. Generally speaking, too fast welding speed will lead to a decrease in weld quality, while too slow speed will reduce production efficiency.
Pulse frequency selection:
In pulse laser welding, the selection of pulse frequency will affect the quality and efficiency of the weld. Higher pulse frequency can increase the welding speed, but may cause excessive heat input to the weld, resulting in welding defects.
The selection of pulse frequency needs to be comprehensively considered according to the characteristics of the material and welding requirements.
2.Improve the preparation work before welding
Material cleaning and treatment:
Before welding, the material must be thoroughly cleaned to remove impurities such as oil, rust, and moisture on the surface. Chemical cleaning, mechanical grinding and other methods can be used for cleaning.
For some special materials, surface treatment is also required. For example, before aluminum alloy welding, anodizing can be performed to improve the welding quality.
Selection and control of shielding gas:
Select the appropriate shielding gas according to the type of welding material and the requirements of the welding process. For example, for stainless steel welding, argon is usually used as the shielding gas; for aluminum alloy welding, a mixture of argon and helium can be used.
Strictly control the flow and purity of the shielding gas. Gas flow meters and gas purity detectors can be used to ensure the quality of the shielding gas.
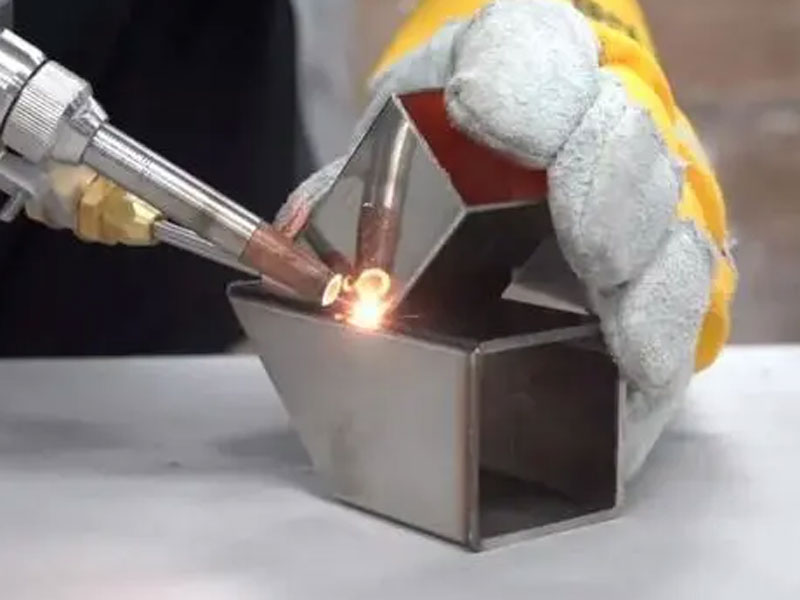
3.Equipment maintenance and upgrade
Maintenance points of laser generator:
- Regularly check the optical system of the laser generator, such as the cleanliness and damage of the lens. If the lens is contaminated or damaged, it will affect the output power and quality of the laser.
- Maintain the power supply system of the laser generator to ensure the stability and reliability of the power supply. Power supply fluctuations may cause unstable laser output, thus affecting the welding quality.
Calibration and replacement of welding heads:
- The position and angle of the welding head have a great influence on the welding quality. Calibrate the welding head regularly to ensure that its relative position and angle with the welding workpiece are accurate.
- When the welding head is worn or damaged, replace it in time to ensure the welding quality.
Conclusion
With the continuous advancement of science and technology, laser welding technology will continue to develop and improve. In the future, laser welding technology will be more intelligent and can automatically monitor and adjust welding parameters to meet the requirements of different materials and welding processes. At the same time, new laser welding equipment and materials will continue to emerge, providing more possibilities for the development of laser welding technology.
FAQ
How strong is laser welding
Laser welding generally produces stronger welds than conventional TIG welding. This is because laser welding focuses the heat into a smaller area, resulting in a narrower heat-affected zone and less material deformation, resulting in a stronger weld.
Is laser welding stronger than tig
Yes. The high energy density and precise control of laser welding give it an advantage in producing strong welds. Which welding method is more suitable depends on many factors, such as material, thickness, and the required weld quality.