In the field of industrial manufacturing, cutting accuracy and efficiency are very important. The numerical control laser pipe cutting machine is at the forefront, and such superb technology and speed can complete the rapid cutting of metal pipes.
This blog will delve into the secrets behind metal tube cutting machines and see how numerical control laser tube cutting machines achieve precision and ingenuity.
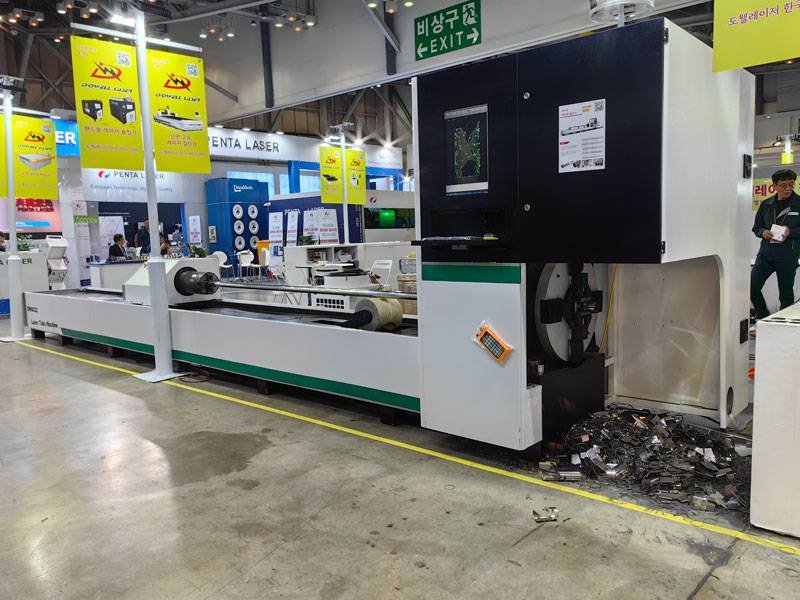
Understanding CNC Laser Tube Cutting Machines
CNC laser tube cutting machines are a revolutionary tool in the world of manufacturing. These machines utilize advanced laser technology to precisely cut and shape metal tubes with unparalleled accuracy. By harnessing the power of lasers, manufacturers can achieve intricate designs and complex cuts that were once thought impossible.
One of the key components of CNC laser tube cutting machines is the computer numerical control (CNC) system. This system allows operators to program specific cutting patterns and dimensions, ensuring consistent and precise results every time. With the ability to create intricate designs and complex shapes, these machines have opened up a world of possibilities for manufacturers across various industries.
Whether it’s automotive parts, aerospace components, or architectural elements, CNC laser tube cutting machines have become an essential tool for modern manufacturing. The versatility and precision they offer make them an invaluable asset in today’s competitive market.
CNC Laser Tube Cutting Technology Develop
The development of CNC laser tube cutting technology has come a long way since its inception. In the early days, these machines were limited in their capabilities and were primarily used for simple cuts on thin materials.
However, advancements in laser technology and computer programming have transformed CNC laser tube cutting machines into highly sophisticated tools capable of handling complex tasks. Today’s machines can cut through thick metal tubes with ease while maintaining exceptional precision.
Furthermore, the integration of CAD/CAM software has streamlined the design process, allowing manufacturers to create intricate patterns and shapes effortlessly. This level of automation has significantly reduced production time and increased overall efficiency.
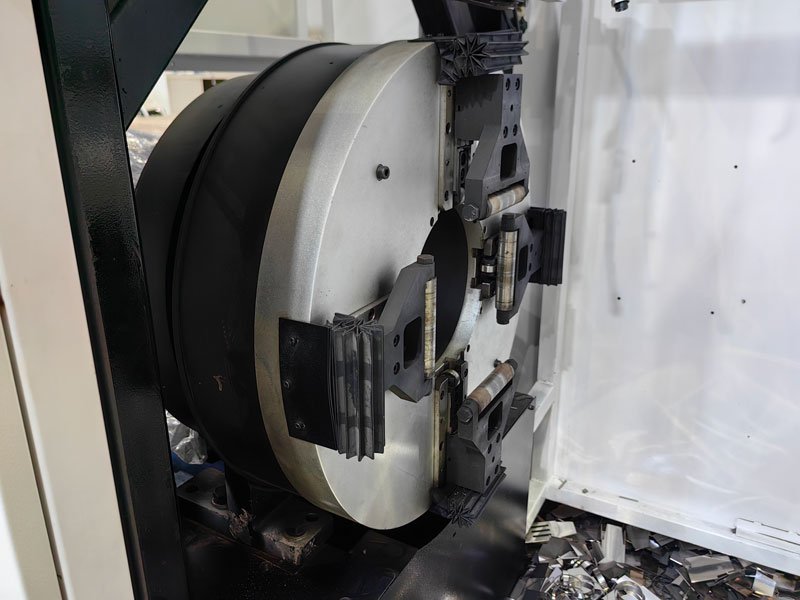
Benefits of Using CNC Laser Tube Cutting Machines
Numerous advantages come with the utilization of CNC laser tube cutting machines. A key benefit is their capability to deliver precise cuts while minimizing material wastage. Unlike conventional cutting techniques that often result in substantial material loss, cnc fiber laser tube cutting machine streamline the cutting process, hence reducing waste and cutting down on costs.
Moreover, these machines boast remarkable speed and accuracy. Equipped with high-powered lasers and sophisticated control systems, they can effortlessly slice through metal tubes with unparalleled precision, ensuring consistent outcomes every single time. This level of precision is particularly critical in sectors where even the slightest deviation can translate into expensive mistakes.
Furthermore, the versatility of cnc fiber laser tube cutting machine is worth noting. They can process a broad array of materials, ranging from stainless steel and aluminum to brass and more. This adaptability renders them suitable for a diverse range of industries and applications.
Factors to Consider Before Mastering CNC Laser Tube Cutting
Before diving into the world of CNC laser tube cutting machines, there are several factors to consider. First and foremost is the initial investment cost. These machines can be quite expensive, So assessing your budget costs is very important in manufacturing.
Another factor to consider is the size and capacity of the machine. Depending on your production requirements, you may need a machine that can handle larger or smaller tubes. It is important to choose a machine that meets your specific needs to maximize efficiency.
In addition to size and capacity, another point to evaluate the machine is its software compatibility. Ensure that the CAD/CAM software you use is compatible with the CNC laser tube cutting machine you intend to purchase. This will ensure seamless integration and streamline your workflow.
Precision and Accuracy: Key Features of CNC Laser Tube Cutting Machines
Precision and accuracy are two key features that set CNC laser tube cutting machines apart from traditional cutting methods. These machines utilize high-powered lasers guided by advanced control systems to achieve precise cuts with minimal deviation.
The ability to cut complex shapes with exceptional accuracy makes CNC laser tube cutting machines ideal for industries that require intricate designs. Whether it’s creating decorative architectural elements or manufacturing precise automotive parts, these machines deliver consistent results every time.
Furthermore, CNC laser tube cutting machines offer exceptional repeatability. Once a cutting pattern is programmed into the machine, it can reproduce the same results repeatedly without any variation. This level of consistency is crucial in industries where uniformity is paramount.
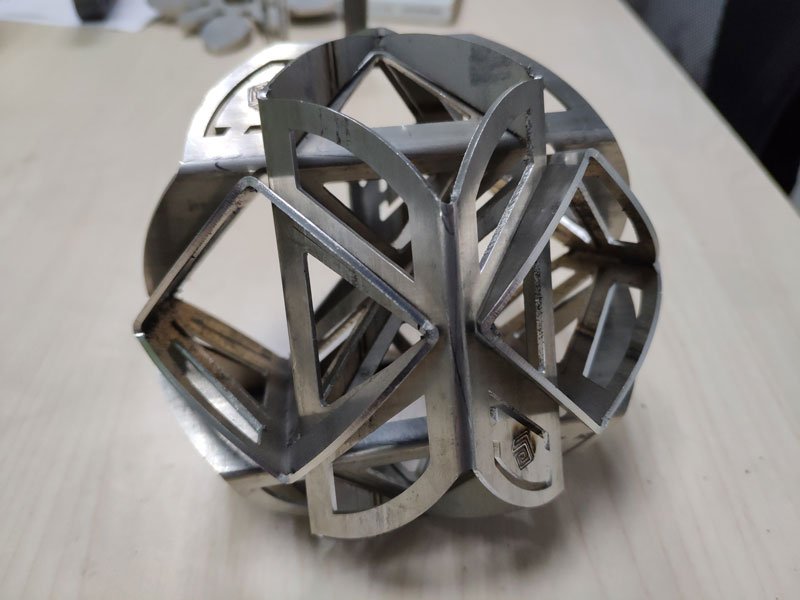
Exploring Advanced Techniques in CNC Laser Tube Cutting
As technology continues to advance, so does the technology used in CNC laser tube cutting. Among them, 3D laser cutting technology can easily create complex three-dimensional shapes.
Another advanced technique is bevel cutting, which involves cutting tubes at an angle to create precise beveled edges. This technique is commonly used in industries such as automotive and aerospace, where beveled edges are required for optimal performance.
Additionally, some CNC laser tube cutting machines offer rotary axis capabilities. This allows for the rotation of tubes during the cutting process, enabling the creation of intricate patterns and designs that would otherwise be impossible.
Maximizing Efficiency with CNC Laser Tube Cutting Machines
To maximize the efficiency of CNC laser tube cutting machines, several strategies can be adopted.
- Nesting optimization involves arranging multiple parts on a sheet of material to minimize waste and maximize productivity.
- Automation and integration with other manufacturing processes. Streamline production lines and reduce manual labor by seamlessly integrating CNC laser pipe cutting machines with other equipment such as robotic arms or conveyor systems.
Maintaining regular maintenance and calibration schedules is also crucial for maximizing efficiency. Regularly inspecting and cleaning the machine’s optics and ensuring proper alignment will help maintain optimal performance and prevent costly downtime.
Applications of CNC Laser Tube Cutting in Various Industries
The applications of CNC laser tube cutting machines span across various industries. In the automotive industry, these machines are used to create exhaust systems, chassis components, and intricate body parts with exceptional precision.
In the aerospace industry, CNC laser tube cutting machines are utilized to manufacture aircraft frames, engine components, and intricate tubing systems. The ability to cut complex shapes and maintain tight tolerances is essential in this industry to ensure the safety and performance of aircraft.
Architectural firms also benefit from CNC laser tube cutting machines. These machines can create decorative elements such as stair railings, ornamental facades, and unique structural components that add a touch of elegance to buildings.
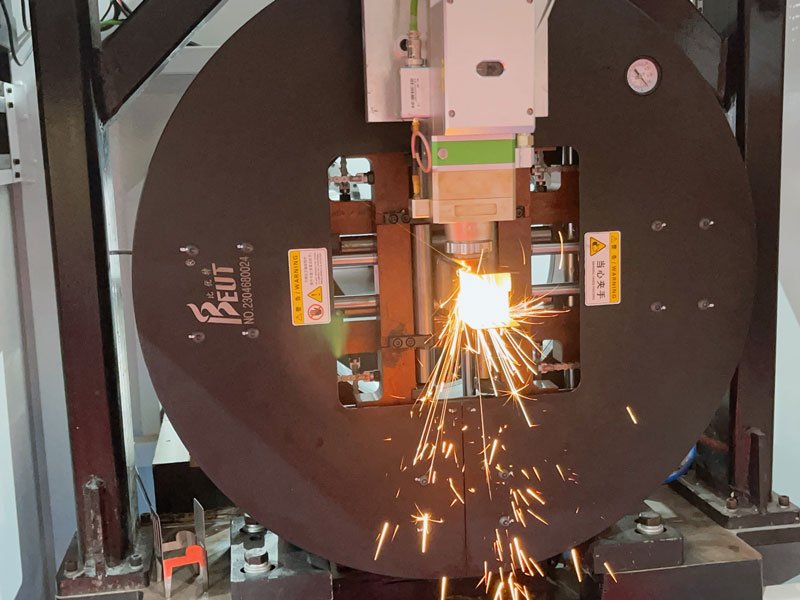
Overcoming Challenges in Mastering CNC Laser Tube Cutting
Mastering CNC laser tube cutting comes with its fair share of challenges. One common challenge is selecting the appropriate laser power for the desired application. Different materials and thicknesses require different laser powers to achieve optimal results.
Another challenge is ensuring proper fixturing of tubes during the cutting process. Tubes must be securely held in place to prevent movement or vibration that could affect the accuracy of cuts. Developing effective fixturing techniques is crucial for achieving consistent results.
Furthermore, understanding and optimizing cutting parameters such as feed rate, power intensity, and assist gas pressure can significantly impact the quality of cuts. Different settings must be tried to find the best parameters for each specific application.
Concluding
CNC laser tube cutting machines have revolutionized modern manufacturing by offering unparalleled precision, efficiency, and versatility. From auto parts to construction, these machines have become indispensable tools in various industries.
As technology continues to advance, the capabilities of CNC laser tube cutting machines will only expand. With the ability to create complex shapes, intricate designs, and precise cuts, these machines empower manufacturers to push the boundaries of what’s possible.
Embracing innovation with CNC laser tube cutting is not just about adopting new technology; it’s about embracing a mindset of continuous improvement and pushing the limits of what can be achieved. By harnessing the power of these advanced machines, manufacturers can unlock new possibilities and stay ahead in today’s competitive market.