This comprehensive guide demystifies the speed and power of découpe au laser, giving you not only insights but also the keys to unlocking a realm of possibilities.
From the novice hobbyist to the experienced craftsman, laser cutting speed and power charts change the way we perceive and utilize this cutting-edge technology. Join us as we decipher the language of lasers and uncover the complex secrets of this powerful tool. The laser cutting speed and power chart will be your compass in the vast sea of creative possibilities.
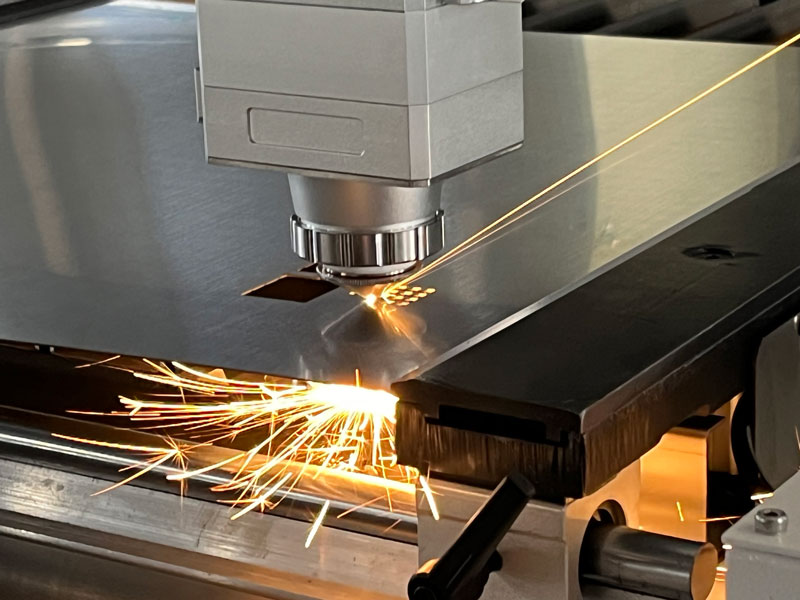
Laser Cutting Speed and Power
In the world of laser cutting, speed and power are two crucial factors that determine the efficiency and precision of the process. The laser cutting speed and power chart serve as a comprehensive guide, providing valuable insights into optimizing these settings for different materials. By understanding the importance of speed and power in laser cutting, as well as the factors influencing them, you can achieve remarkable results in your projects.
Importance of Speed and Power in Laser Cutting
Speed and power play vital roles in laser cutting. Speed refers to how fast the laser beam travels through the material, and power determines the intensity of the beam. Finding the right balance between these two variables is critical to achieving clean cuts, minimizing material waste, and maximizing productivity.
Speed settings:
If set too high, it can cause rough edges or even burn marks on some materials.
Lower speed settings ensure a smoother cut but may significantly increase production time. Power is equally important as it determines how efficiently the laser beam cuts different materials.
Power settings:
Higher power settings are suitable for thicker or denser materials that require more energy to cut effectively.
Lower power settings are ideal for delicate or thin materials to prevent over-burning or melting.
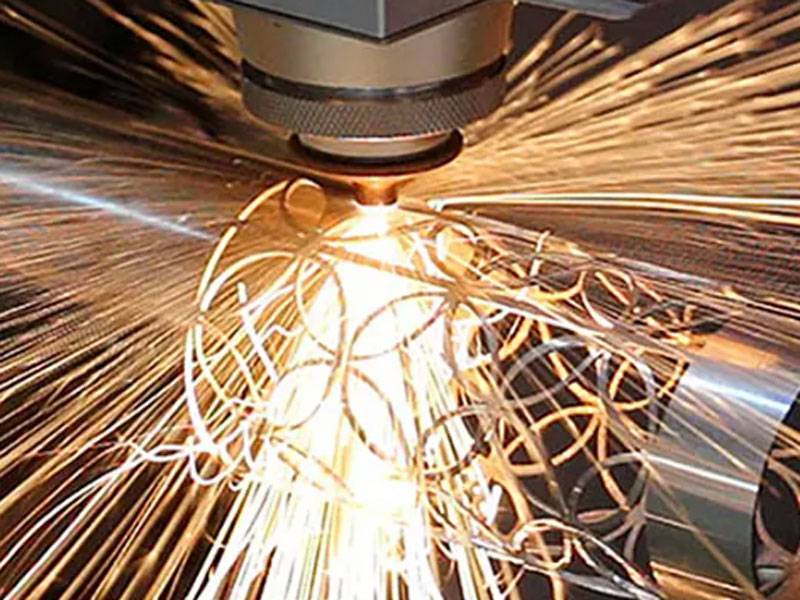
Laser Cutting Speed and Power Chart
Fiber Laser Cutting Speed and Power Chart
Laser Power (W) | Carbon Steel Thickness (mm) | Stainless Steel Thickness (mm) | Aluminum Thickness (mm) | Brass Thickness (mm) |
---|---|---|---|---|
1000W | 0.8 – 10 | 0.8 – 5 | 0.8 – 3 | 1 – 3 |
1500W | 1 – 16 | 1 – 6 | 1 – 4 | 1 – 3 |
2000W | 1 – 20 | 1 – 8 | 1 – 6 | 1 – 5 |
3000W-3300W | 1 – 22 | 1 – 10 | 1 – 8 | 1 – 6 |
4000W | 1 – 25 | 1 – 15 | 1 – 10 | 1 – 8 |
6000W | 1 – 30 | 1 – 20 | 1 – 20 | 1 – 12 |
8000W | 1 – 40 | 1 – 30 | 1 – 30 | 1 – 16 |
10000W | 1 – 45 | 1 – 40 | 1 – 40 | 1 – 20 |
12000W | 1 – 50 | 1 – 45 | 1 – 45 | 1 – 20 |
15000W | 1 – 60 | 1 – 50 | 1 – 40 | 1 – 20 |
Tube Laser Cutting Thickness & Speed Chart
Matériel | Thickness (mm) | 1000W (m/min) | 1500W (m/min) | 2000W (m/min) | 3000W (m/min) | 4000W (m/min) | 6000W (m/min) |
---|---|---|---|---|---|---|---|
Acier Carbone | 1 | 2.0-4.0 | 2.5-4.5 | 3.0-5.0 | 5.0-8.0 | 7.0-10.0 | 8.0-12.0 |
Acier Carbone | 2 | 2.0-4.0 | 2.5-4.5 | 3.0-5.0 | 5.0-8.0 | 7.0-10.0 | 8.0-12.0 |
Acier inoxydable | 1 | 2.0-3.5 | 2.3-3.5 | 2.5-4.0 | 4.0-5.5 | 5.0-7.7 | 6.0-8.7 |
Acier inoxydable | 2 | 2.0-3.5 | 2.3-3.5 | 2.5-4.0 | 4.0-5.5 | 5.0-7.7 | 6.0-8.7 |
Aluminium | 1 | 2.5-4.0 | 3.0-5.0 | 3.5-5.0 | 5.0-7.0 | 6.0-8.0 | 7.0-9.0 |
Aluminium | 2 | 2.5-4.0 | 3.0-5.0 | 3.5-5.0 | 5.0-7.0 | 6.0-8.0 | 7.0-9.0 |
Laiton | 1 | 2.0-3.5 | 2.3-3.5 | 2.5-4.0 | 4.0-5.5 | 5.0-7.7 | 6.0-8.7 |
Laiton | 2 | 2.0-3.5 | 2.3-3.5 | 2.5-4.0 | 4.0-5.5 | 5.0-7.7 | 6.0-8.7 |
CO2 Laser Cutting Thickness & Speed and Power Chart For Steel Plate
Matériel | Steel plate | ||
---|---|---|---|
Thickness | 2mm | 3mm | |
25W | Max Speed | —— | —— |
Optimal speed | —— | —— | |
40W | Max Speed | —— | —— |
Optimal speed | —— | —— | |
60W | Max Speed | —— | —— |
Optimal speed | —— | —— | |
80W | Max Speed | —— | —— |
Optimal speed | —— | —— | |
100W | Max Speed | —— | —— |
Optimal speed | —— | —— | |
130W | Max Speed | —— | —— |
Optimal speed | —— | —— | |
150W | Max Speed | 8mm/s | —— |
Optimal speed | 6mm/s | —— | |
180W | Max Speed | 15mm/s | 7mm/s |
Optimal speed | 12mm/s | —— | |
200W | Max Speed | 40mm/s | 25mm/s |
Optimal speed | 30mm/s | 18mm/s |
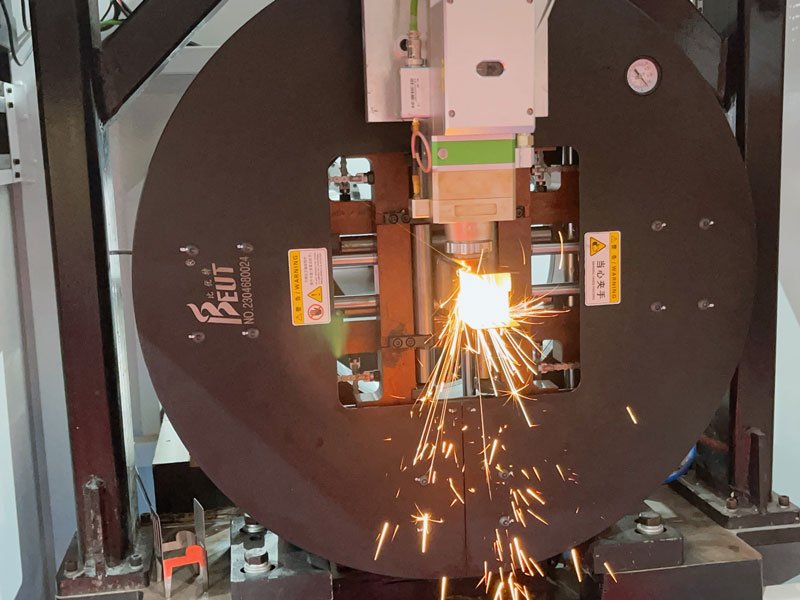
Factors Influencing Laser Cutting Speed and Power
The type and thickness of the material being cut are major considerations. Different materials have different levels of thermal conductivity and absorptivity, which affects their response to laser cutting.
Design complexity also plays a role in determining optimal speed and power settings. Intricate designs with intricate details may require slower speeds to ensure precise cuts without compromising quality.
Focal length (the distance between the lens and the material), auxiliary gas pressure (used to blow away molten material), nozzle diameter (affects the focus of the beam), and lens quality all affect the laser cutting process.
The Science Behind Laser Cutting Speed and Power
Laser cutting works on the principle of localized heating. The laser beam heats a small area of material, causing it to melt or vaporize.
The focused beam moves along a designated path, cutting materials with precision. The speed at which the laser beam moves determines how much heat is applied to a specific area.
The higher the speed, the more even the heat is distributed, preventing excessive melting or burning.
Slower speeds apply heat more concentratedly, resulting in cleaner cuts.
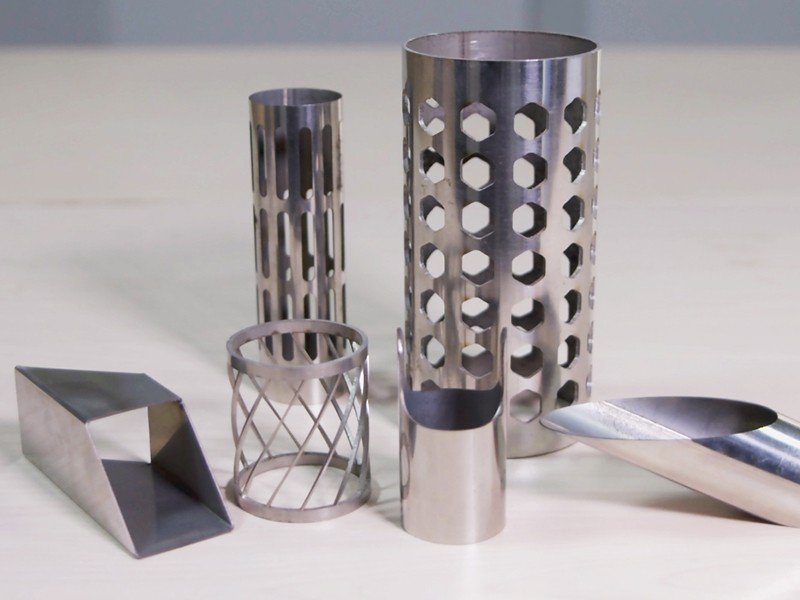
Speed and Power Settings for Different Materials
Different materials require specific speed and power settings for best results.
- Metal may require higher power settings and moderate speeds to ensure a clean cut without excessive burning.
- Wooden materials generally respond well to moderate power settings and faster speeds because they absorb less heat than metal or plastic.
When working with new materials, it is important to refer to the manufacturer’s guidelines or perform tests to determine the best speed and power settings for your laser cutter.
Achieving Precision: Fine-Tuning Speed and Power
Fine-tuning speed and power settings are crucial to achieving precise cuts in your laser cutting projects. Experimentation is key when working with different materials or designs.
Test a small section of the material using different speed and power combinations until you find the best settings that produce a clean cut without compromising quality.
Certain factors may require adjusting speed and power settings throughout the project. For example, complex designs may require slower speeds in detailed areas while maintaining faster speeds elsewhere.
Maximizing Speed and Power Efficiency
To maximize efficiency in laser cutting projects, several advanced techniques can be employed alongside optimal speed and power settings:
- Nesting: This technique involves arranging multiple parts on a single sheet of material to minimize waste and increase productivity.
- Pierce time optimization: By adjusting the pierce time (the duration it takes for the laser beam to penetrate the material), you can reduce production time without compromising on quality.
- Kerf compensation: The laser beam removes a small amount of material during cutting, resulting in a wider cut than intended. By compensating for this kerf width, you can achieve more accurate cuts.
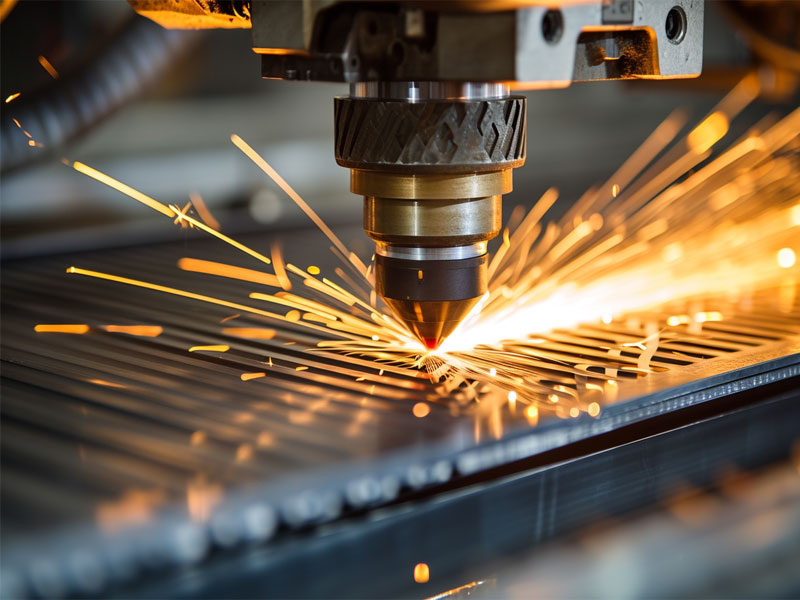
Enhancing Productivity Through Laser Cutting Speed and Power
The laser cutting speed and power chart serves as an invaluable tool for enhancing productivity in your projects. By understanding the dynamics of speed and power, as well as the factors influencing them, you can optimize your laser cutter’s performance across various materials. Whether you are a beginner enthusiast or a seasoned craftsman, harnessing the true potential of laser cutting requires mastery over speed and power settings. With the right knowledge and guidance provided by the laser cutting speed and power chart, you can unlock a world of creative possibilities while achieving precision and efficiency in your projects.
Conclusion:
Mastering laser cutting speed and power is critical to achieving excellent results on your projects. The laser cutting speed and power chart serve as a comprehensive guide, giving you insight into optimizing these settings for different materials.
You can take your laser cutting skills to new heights by understanding the importance of speed and power, considering the factors that affect them, fine-tuning settings for precision, employing advanced techniques, and increasing productivity through efficient use of speed and power.
FAQ
What Can and Cant a Laser Cut Through?
Laser cutters can easily cut through materials such as paper, wood, acrylic, and even some metals. However, the scope of laser cutting is limited. For example, highly reflective materials such as copper and aluminum can be challenging to laser cut. Additionally, high melting point materials, such as diamond and certain ceramics, are not suitable for laser cutting.
What Is the Future of Laser Cutting?
Innovations in laser sources and control systems are improving efficiency and precision. Today’s laser cutting machines offer higher power options and faster processing speeds, making them ideal for a wide range of applications across a variety of industries.
How Many Types of Laser Cutting Are Used in Industries?
Types include CO2 laser cutting, fiber laser cutting, and neodymium (Nd) laser cutting.
CO2 lasers are best at cutting non-metallic materials like wood and plastic, while fiber lasers excel at cutting metals with high precision. Neodymium lasers are known for their high power output, making them ideal for cutting thick materials.