In the evolving landscape of manufacturing, tube laser processing machines stand out as a groundbreaking innovation, blending advanced laser technology with automated precision to transform the way industries cut, shape, and fabricate metal tubes. These machines have revolutionized the fabrication sector, providing unparalleled accuracy, speed, and versatility.
This article delves into the intricacies of tube laser processing machines, exploring their technology, applications, benefits, and future prospects.
What is a Tube Laser Processing Machine?
UN tube laser processing machine is a sophisticated piece of equipment that uses laser technology to cut, engrave, and mark tubular materials with exceptional accuracy. Unlike traditional cutting methods, laser processing offers unparalleled precision, speed, and flexibility, making it an indispensable tool in modern manufacturing.
Components of a tube laser processing machine
- Source laser: The heart of the machine, generating the laser beam. Fiber lasers are preferred for their high efficiency and ability to cut through thicker materials.
- CNC Control System: Ensures precision by controlling the movement of the laser and the tube.
- Clamping and Rotating Mechanism: Holds and rotates the tube to achieve multi-dimensional cuts.
- Tête de coupe: Directs the laser beam and can be adjusted for different angles and depths of cut.
- Software: Advanced software solutions are used to design cutting patterns and optimize the cutting process.
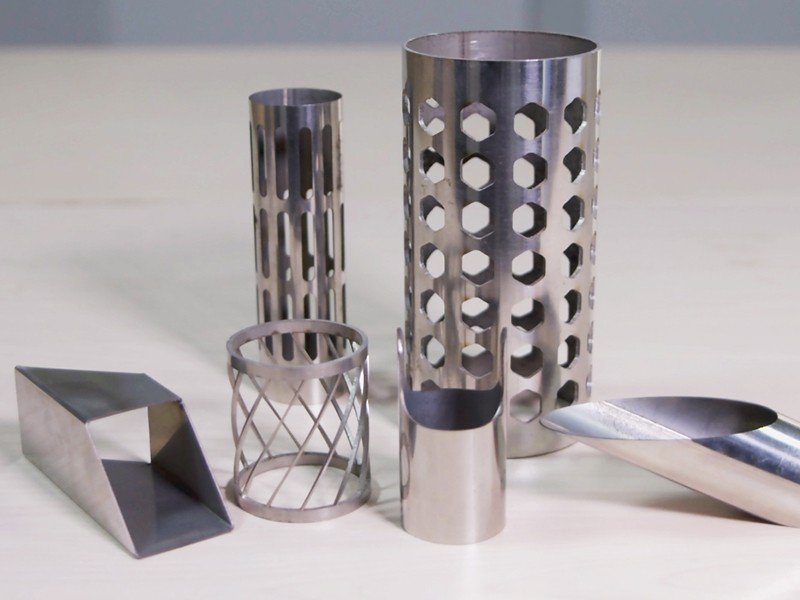
Advantages of Tube Laser Processing
1. Unmatched Precision
Tube laser processing machines can achieve cutting accuracies of up to ±0.1mm, ensuring consistent quality across large production runs. This level of precision is crucial for industries où even the slightest deviation can lead to significant issues.
2. Versatility in Material Handling
These machines can process a wide range of materials, including:
- Acier inoxydable
- Acier Carbone
- Aluminium
- Cuivre
- Laiton
- And various alloys
This versatility makes tube laser processing machines adaptable to diverse fabrication besoins.
3. Complex Cutting Capabilities
One of the most significant advantages of tube laser processing is its ability to perform intricate cuts and shapes that would be impossible or extremely difficult with traditional methods. From precise holes to complex patterns, these machines can handle it all.
4. Increased Productivity
With high-speed processing capabilities and minimal setup time, tube laser machines significantly boost productivity. Many models can operate 24/7, further enhancing output.
5. Cost-Effectiveness
While the initial investment may be substantial, tube laser processing machines offer long-term cost savings through:
- Réduction des déchets de matériaux
- Lower labor costs
- Decreased need for secondary operations
- Improved energy efficiency
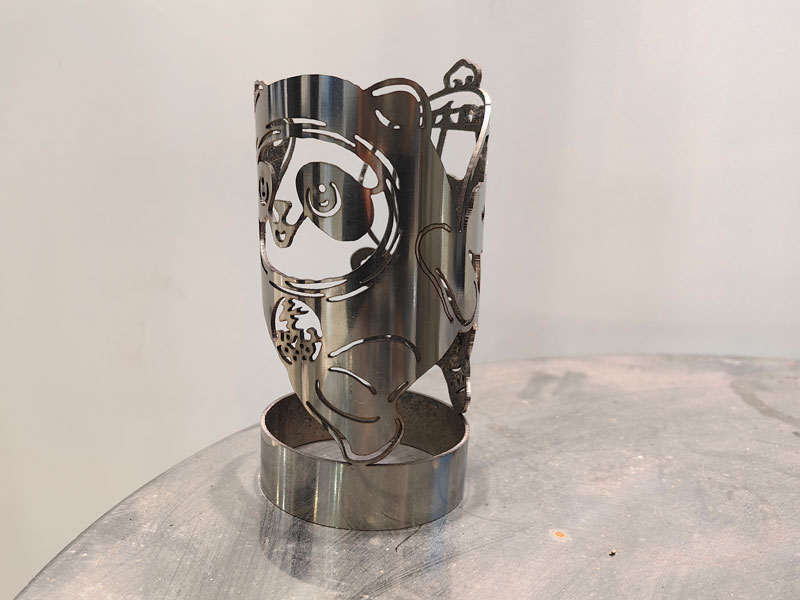
Applications of Tube Laser Processing Machines
Automotive Industry: Used for cutting and shaping exhaust systems, chassis components, and other structural parts. The precision of laser cutting ensures the durability and safety of automotive components.
Aerospace Industry: Essential for fabricating lightweight and strong components, such as aircraft frames and engine parts. The accuracy of laser cutting is crucial for maintaining the structural integrity of aerospace components.
Construction Industry: Employed in the creation of steel frameworks, railings, and structural beams. The ability to cut complex shapes and designs enhances architectural possibilities.
Furniture Manufacturing: Enables the production of aesthetically pleasing and functional furniture pieces, such as metal chairs, tables, and decorative elements. The versatility of laser cutting allows for unique and intricate designs.
Medical Equipment: Used in the production of medical devices and instruments that require high precision and reliability. Laser cutting ensures the quality and safety of medical components.
Renewable Energy Sector: Essential in manufacturing components for wind turbines, solar panels, and other renewable energy systems. The precision of laser cutting contributes to the efficiency and reliability of renewable energy solutions.
Technological Advancements in Tube Laser Processing
The continuous evolution of tube laser processing technology has led to several advancements that enhance its capabilities and performance:
- Improved Laser Sources: Advances in fiber laser technology have resulted in higher power outputs and greater efficiency. Modern fiber lasers offer better beam quality, enabling faster and more precise cutting.
- Enhanced CNC Systems: The integration of advanced CNC control systems allows for more complex and intricate cutting patterns. These systems provide greater flexibility and control over the cutting process.
- Automated Loading and Unloading: Automation of the material handling process reduces downtime and increases productivity. Automated loading and unloading systems ensure a seamless and efficient workflow.
- Real-Time Monitoring and Feedback: Modern tube laser processing machines are equipped with sensors and monitoring systems that provide real-time feedback on the cutting process. This ensures optimal performance and quality control.
- Hybrid Machines: Combining laser cutting with other machining processes, such as bending and welding, to create hybrid machines that offer multi-functional capabilities. These machines streamline the manufacturing process by combining multiple operations into a single machine.
- Software Integration: Advanced software solutions enable seamless integration with CAD/CAM systems, facilitating the design and execution of complex cutting patterns. Software updates and improvements continue to enhance the capabilities of tube laser processing machines.
How Choosing the Right Tube Laser Processing Machine
- Material Types: Ensure the machine can handle the materials you work with most frequently.
- Tube Sizes: Check the maximum and minimum tube dimensions the machine can process.
- Cutting Speed and Power: Higher power generally means faster cutting, but it’s not always necessary for every application.
- Software Compatibility: Look for machines with software that integrates well with your existing systems.
- Automation Features: Consider how much automation you need to optimize your workflow.
- Service and Support: Reliable after-sales support is crucial for maintaining productivity.
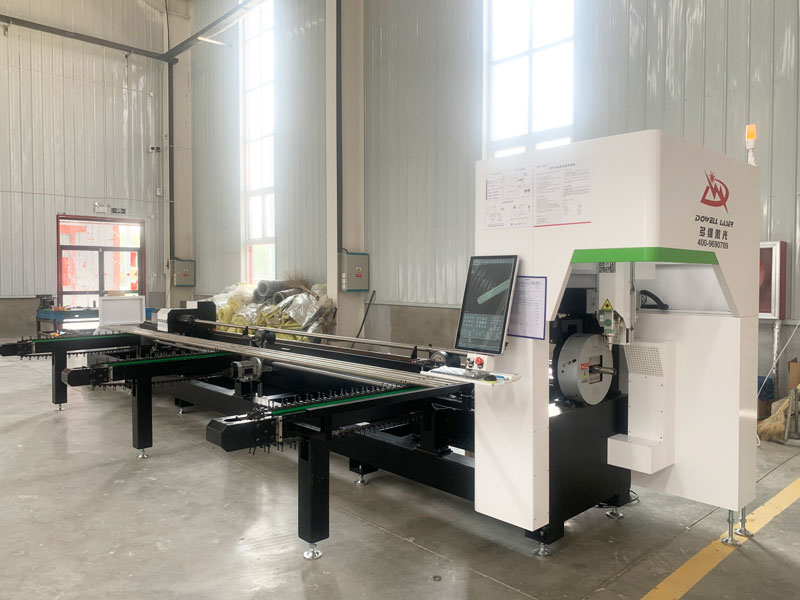
The Future of Tube Laser Processing
As we look to the future, several trends are likely to shape the evolution of tube laser processing:
- Integration with Industry 4.0: Expect to see more machines with IoT capabilities, allowing for real-time monitoring and predictive maintenance.
- Increased Energy Efficiency: Future machines will likely consume even less energy while maintaining or improving performance.
- Advancements in Laser Technology: Ongoing research and development in laser technology will lead to more powerful and efficient lasers. These advancements will expand the range of materials that can be processed and improve the overall performance of tube laser processing machines.
- Enhanced Artificial Intelligence: AI integration could lead to machines that can optimize cutting parameters in real-time based on material properties and desired outcomes.
- Expanded Material Capabilities: Research is ongoing to expand the range of materials that can be effectively processed, including more exotic alloys and composites.
- Sustainability Focus: As industries prioritize sustainability, tube laser processing machines will play a crucial role in reducing material waste and energy consumption.
- Customization and Personalization: The demand for customized and personalized products is on the rise. Tube laser processing machines will enable fabricants to produire bespoke designs and tailor-made solutions to meet individual customer needs.
Conclusion:
Tube laser processing machines have revolutionized the manufacturing industry, offering unmatched precision, speed, and versatility. Their ability to cut complex shapes and designs with minimal material waste has made them indispensable across various sectors, from automotive to aerospace and beyond.
As technology continues to advance, these machines will become even more efficient and capable, driving innovation and sustainability in manufacturing.
Investing in tube laser processing technology is not just a step towards modernizing manufacturing processes; it is a leap towards achieving higher productivity, superior quality, and a more sustainable future.
Whether you are in the automotive industry, construction, furniture manufacturing, or any other sector that requires precision cutting and shaping of metal tubes, tube laser processing machines are the key to unlocking new possibilities and staying ahead in a competitive market.