Cutting stainless steel is a crucial task in various industries, from construction to automotive fabrication. The choice of tool impacts not only the quality of the cut but also the efficiency and safety of the process. In this article, we’ll explore the best tools for cutting stainless steel, detailing their uses, advantages, and limitations to help you make an informed decision.
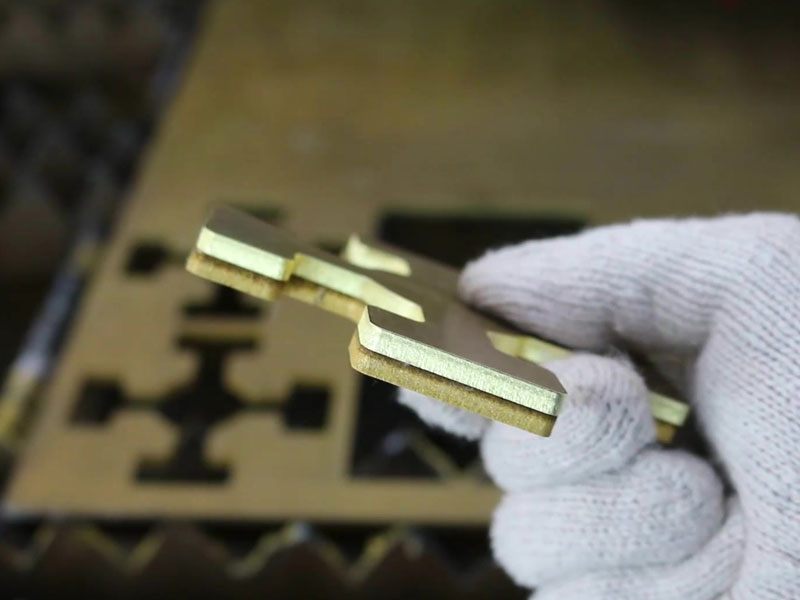
Types of Cutting Tools
Manual Tools
Hacksaw
A hacksaw is a hand tool with a thin, fine-toothed blade set in a frame. It’s ideal for small-scale cutting tasks and intricate work. While it requires manual effort, it offers precision and control.
Tin Snips
Tin snips are scissor-like tools designed for cutting thin sheets of metal. They come in different types, including straight-cut, left-cut, and right-cut snips, each suited for specific cutting directions.
Power Tools
Angle Grinder
An angle grinder is a versatile power tool equipped with a rotating disc. It’s suitable for cutting, grinding, and polishing metal surfaces. With various disc types available, it’s adaptable to different cutting needs.
Circular Saw
A circular saw uses a toothed or abrasive disc to cut materials. Quand fitted with a metal-cutting blade, it’s effective for straight cuts through stainless steel.
Advanced Cutting Tools
Laser Cutter
Laser cutting employs a high-powered laser to melt or vaporize material, offering precise cuts with minimal waste. It’s highly effective for detailed and intricate designs.
Plasma Cutter
A plasma cutter uses a jet of hot plasma to cut through electrically conductive materials. It’s fast and efficient, making it suitable for thicker stainless steel sheets.
Hacksaw
Description and Usage
A hacksaw consists of a blade mounted on a frame, used primarily for cutting metal. The blade’s fine teeth make it suitable for precise cuts.
Pros and Cons
Avantages:
- Precise cutting
- Inexpensive
- No electricity required
Les inconvénients:
- Slow process
- Manual effort required
Best Practices
- Use steady, even strokes
- Ensure the blade is tensioned correctly
- Replace worn blades promptly
Tin Snips
Types of Tin Snips
- Straight-Cut Snips: Ideal for straight cuts and wide curves.
- Left-Cut Snips: Designed for making left curves.
- Right-Cut Snips: Best for right curves.
Pros and Cons
Avantages:
- Easy to use
- No power source needed
- Suitable for detailed cuts
Les inconvénients:
- Limited to thin sheets
- Can cause jagged edges
Best Practices
- Keep blades sharp
- Use appropriate snips for the cut direction
- Avoid overextending the tool
Angle Grinder
Description and Usage
An angle grinder features a rotating disc for cutting, grinding, and polishing. It’s highly versatile and powerful, making it suitable for a variety of cutting tasks.
Types of Discs
- Cutting Discs: Thin and ideal for cutting through metal.
- Grinding Discs: Thicker and used for smoothing surfaces.
- Polishing Discs: For finishing touches and polishing.
Pros and Cons
Avantages:
- Versatile
- Fast cutting speed
- Suitable for various metals
Les inconvénients:
- Generates sparks and noise
- Requires safety precautions
Safety Tips
- Wear protective gear (gloves, goggles, ear protection)
- Ensure the disc is securely attached
- Work in a well-ventilated area
Circular Saw
Description and Usage
A circular saw is a power tool with a rotating blade, effective for making straight cuts in stainless steel quand equipped with a suitable blade.
Types of Blades
- Carbide-Tipped Blades: Durable and effective for cutting metal.
- Abrasive Blades: Thin and ideal for slicing through metal sheets.
Pros and Cons
Avantages:
- Fast and efficient
- Suitable for straight cuts
- High precision
Les inconvénients:
- Can be bulky
- Requires careful handling
Safety Tips
- Wear safety gear
- Secure the material before cutting
- Follow the fabricant‘s guidelines
Laser Cutter
How Laser Cutting Works
Laser cutting uses a focused laser beam to melt or vaporize material, providing high precision and clean cuts with minimal waste.
Advantages of Laser Cutting
- High precision
- Minimal waste
- Suitable for complex designs
Suitable Applications
- Detailed and intricate designs
- High-precision tasks
- Industrial and artistic applications
Safety Considerations
- Use appropriate eye protection
- Ensure proper ventilation
- Follow safety protocols
Plasma Cutter
How Plasma Cutting Works
Plasma cutting involves a jet of hot plasma to cut through electrically conductive materials. It’s fast and efficient, making it ideal for thicker sheets.
Advantages of Plasma Cutting
- Fast cutting speed
- Suitable for thick materials
- Clean cuts
Suitable Applications
- Wo kann ich eine 1000-W-Faserlaserschneidemaschine kaufen? China lightweld 1500 laser welding manufacturer
- Repair and maintenance
- Art and sculpture
Safety Considerations
- Wear protective gear
- Ensure proper ventilation
- Follow safety guidelines
Factors to Consider Quand Choisir un outil de coupe
Épaisseur de matériau
Thicker materials require more powerful tools like plasma cutters or angle grinders, while thinner sheets can be handled with tin snips or hacksaws.
Precision Requirements
For intricate and detailed work, laser cutters and hacksaws are preferable due to their precision.
Rapidité et efficacité
Power tools like angle grinders and plasma cutters are ideal for fast, large-scale projects.
Budget Constraints
Consider initial investment and maintenance costs. Manual tools are cheaper but require more effort, while advanced tools like laser cutters have higher upfront costs but greater efficiency.
Comparison of Cutting Tools
Manual vs. Power Tools
Manual tools are inexpensive and precise but slow and labor-intensive. Power tools offer speed and efficiency but come at a higher cost and require safety measures.
Power Tools vs. Advanced Tools
Advanced tools like laser and plasma cutters provide high precision and speed but require significant investment and safety precautions compared to standard power tools.
Cutting Techniques
Straight Cuts
Use a circular saw or angle grinder with a metal-cutting blade for clean, straight cuts.
Curved Cuts
Tin snips and hacksaws are ideal for curved cuts due to their maneuverability.
Detailed Cuts
Laser cutters are best for detailed and intricate designs due to their precision.
Safety Tips
Personal Protective Equipment
Always wear gloves, safety goggles, and ear protection quand cutting stainless steel.
Handling and Maintenance of Tools
Regularly check and maintain tools to ensure they are in good working condition.
Maintenance of Cutting Tools
Cleaning and Storage
Keep tools clean and store them in a dry, secure place to prevent rust and damage.
Sharpening and Replacing Blades
Regularly sharpen blades and replace them quand they become dull to maintain cutting efficiency.
Cost Analysis
Investissement initial
Consider the initial purchase cost of the tool and any necessary accessories.
Maintenance Costs
Account for ongoing costs like blade replacements and tool maintenance.
Cost-Effectiveness Over Time
Evaluate the long-term benefits and efficiency of the tool in relation to its cost.
Environmental Considerations
Energy Consumption
Advanced tools like laser and plasma cutters consume more energy compared to manual and standard power tools. It’s important to factor in energy costs and efficiency quand choosing the right tool.
Waste Management
Efficient cutting tools produce less waste, which is beneficial for both the environment and cost savings. Tools like laser cutters minimize scrap, reducing overall waste.
Innovations in Cutting Technology
Recent Advancements
- Fiber Laser Technology: Enhances cutting speed and precision, especially for intricate designs.
- Waterjet Cutting: Uses high-pressure water mixed with abrasive materials for precise cuts without heat distortion.
- Automated Cutting Systems: Integration of CNC (Computer Numerical Control) systems for automated and highly accurate cuts.
Future Trends
- AI Integration: Artificial Intelligence is being integrated to optimize cutting patterns and reduce waste.
- Green Technologies: Development of eco-friendly cutting methods to reduce environmental impact.
Case Studies
Successful Projects Using Different Tools
- Industrie automobile : Use of laser cutters for precise and efficient fabrication of car parts.
- Construction: Plasma cutters for fast and effective on-site adjustments and coutume fittings.
- Art and Design: Artists employing hacksaws and tin snips for detailed metal sculptures.
Expert Insights
Quotes from Industry Professionals
- “Laser cutters have revolutionized our production line, allowing us to achieve unparalleled precision and efficiency.” – John Doe, Fabrication Engineer.
- “For thick stainless steel, plasma cutting is unbeatable in terms of speed and quality.” – Jane Smith, Fabrication Specialist.
Tips and Tricks
- “Always use the right blade or disc for the material you’re cutting to ensure clean cuts and prolong tool life.”
- “Regular maintenance of cutting tools is essential to maintain their performance and safety.”
FAQs
What is the best tool for cutting thick stainless steel?
Plasma cutters are ideal for thick stainless steel due to their fast and efficient cutting capabilities.
Can I use a regular saw blade for cutting stainless steel?
No, you should use a blade specifically designed for cutting metal to ensure clean cuts and avoid damaging the tool.
How do I prevent jagged edges quand cutting stainless steel?
Using the correct cutting tool and blade, and ensuring the tool is sharp and well-maintained, will help prevent jagged edges.
Is laser cutting safe for all types of stainless steel?
Yes, laser cutting is safe for most types of stainless steel, but always follow safety protocols and use appropriate protective equipment.
What are the benefits of using a laser cutter for stainless steel?
Laser cutters offer high precision, minimal waste, and the ability to create intricate designs with clean edges.
Conclusion
Cutting stainless steel efficiently and effectively requires choosing the right tool for the job. From manual tools like hacksaws and tin snips to advanced options like laser and plasma cutters, each tool has its advantages and suitable applications. Consider factors such as material thickness, precision requirements, speed, and budget quand selecting a cutting tool. By following best practices and safety tips, you can achieve clean, precise cuts while maintaining tool performance and safety.