After purchasing the laser tube cutting machine, many customers will encounter some common problems during the use of the machine due to improper operation. This article will give specific suggestions and solutions around tube laser cutter problems.
The reasons why the laser tube cutting machine cannot cut may involve many aspects, including the beam quality of the laser, the accuracy of the worktable, the material of the workpiece being cut, the pressure of the auxiliary gas, and the debugging of the laser tube cutting machine.
Why can’t the laser tube cutting machine cut continuously?
- Reasons for water vapor on the protective lens
During the operation of the laser cutting machine, the role of the auxiliary gas is to blow away the residual waste slag to achieve the best cutting effect. The gas blows away the metal slag while protecting the lens to prevent the slag from sticking to the lens and affecting the cutting quality.
During the operation of the laser equipment, if there is moisture on the protective lens, the laser energy is large and the temperature is high, and the protective lens will burst immediately when it encounters water. The appearance of water vapor on the protective lens is an issue that needs attention.
- Reasons for light decay of the protective lens
The protective lens is a very important precision component in the optical path system of the laser cutting machine, which has a great impact on the processing performance and quality of the laser cutting machine. When the protective lens has light decay, it will affect the effect and accuracy of laser cutting.
There are many reasons for the light decay of the protective lens, such as incorrect cutting parameter settings, focal length, cutting speed and plate thickness, air pressure stability and other factors will affect the optical performance of the protective lens.
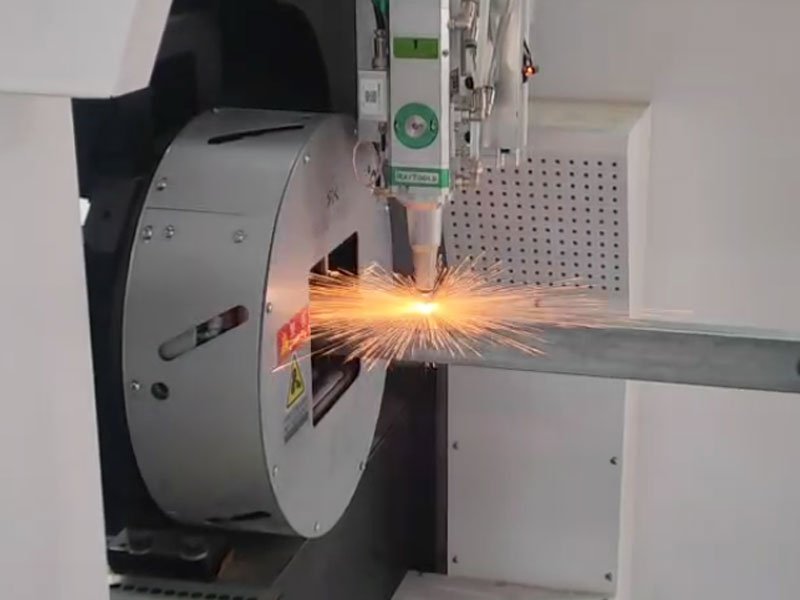
- Reasons for too small cutting power adjustment
The cutting power is one of the very important parameters in the cutting process of the laser cutting machine. If the cutting power is adjusted too small, the laser cutting effect will be poor, the cutting speed will be slow, and even the cutting task cannot be completed.
When operating the laser cutting machine, it is necessary to reasonably adjust the cutting power according to different materials and cutting requirements.
- Reasons for not using shielding gas
In the laser cutting process, shielding gas plays a very important role. Not using shielding gas or shielding gas is impure and the pressure does not meet the standard will lead to poor laser cutting effect and even damage the protective lens of the laser cutting machine.
In the laser cutting process, pure and pressure-compliant shielding gas is required.
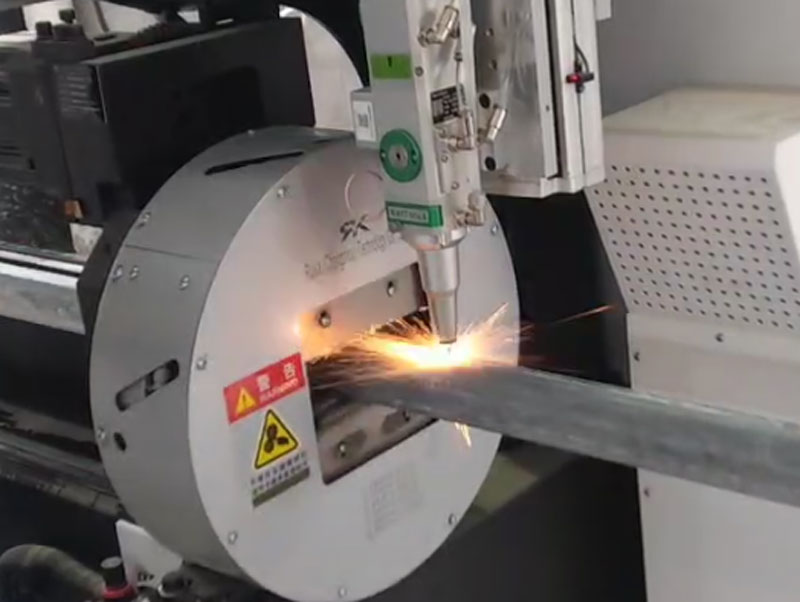
Laser cut quality troubleshooting:Rough cutting surface
If the quality of the tube is poor, the laser may not be able to cut it. For example, if the tube is too hard or too thin, the laser may not be able to cut it or the cutting effect may be poor. In addition, the uneven surface of the tube or the radius is too small may also affect the laser cutting effect.
Insufficient laser power: The laser power is set too low and cannot fully penetrate the material, resulting in a rough and uneven cut surface. You can try to increase the laser power.
Too fast cutting speed: If the cutting speed is too fast, the laser cannot fully melt the material, which may also cause a rough cut surface. You can try to reduce the cutting speed.
Inaccurate focus position: If the laser focus position deviates from the optimal position, it may affect the cutting effect and cause a rough cut surface. The laser focus position needs to be adjusted.
Auxiliary gas problem: If the pressure, flow rate or type of the auxiliary gas is not appropriate, it may affect the cutting effect. For example, when cutting with oxygen, if the gas pressure is too low, the cut surface may be rough. The parameters of the auxiliary gas need to be adjusted.
Material problem: If there is dirt, rust, coating, etc. on the surface of the material, or if the material quality is poor, it may also cause a rough cut surface. It is necessary to clean the surface of the material or replace it with high-quality materials.
Mechanical vibration: If the stability of the machine tool is not good, or mechanical vibration occurs during the cutting process, it may also cause a rough cut surface. The stability of the machine tool needs to be checked and adjusted.
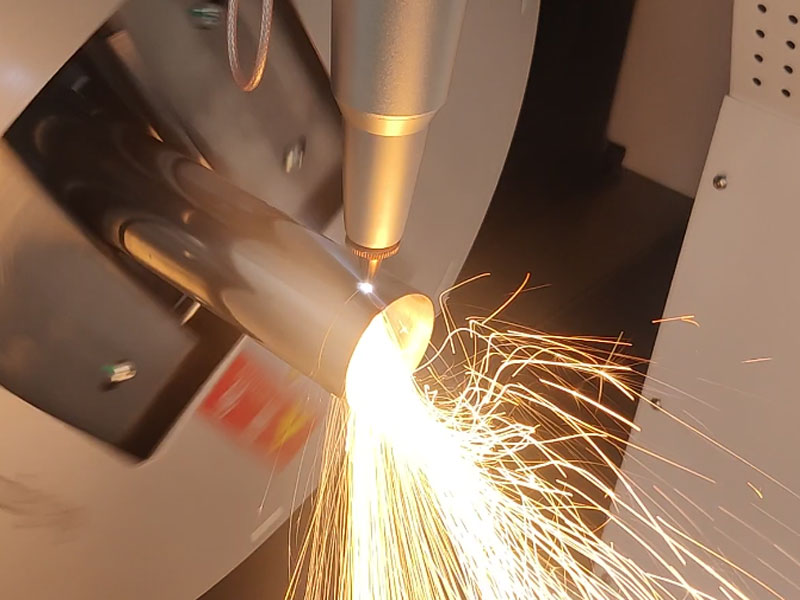
Poor cutting effect or no cutting
- Problem description: Poor cutting effect or no cutting is one of the common problems of laser cutting machines. This may be caused by low power setting, optical path offset, dirty lens, reverse installation of focusing lens, improper focal length, laser tube power attenuation, high water temperature or unstable voltage.
- Solution: Check the power setting: Make sure the power setting is correct and adjust the power size according to the thickness and properties of the material;
Clean the lens: Clean the lens regularly to ensure that the optical path is unobstructed;
Check the focusing system: Make sure the focusing lens is installed correctly and the focal length is adjusted accurately;
Check the laser tube: If the laser tube power attenuation is serious, it needs to be replaced in time;
Stabilize the voltage and water temperature: Make sure the power supply voltage is stable, the cooling system works normally, and the water temperature is not too high.
Unable to connect
- Problem description: The inability to connect the device is another common problem, which may be caused by the board driver not being installed, the USB cable or network cable not being plugged in, the cable being damaged, or the adapter board being faulty.
- Solution: Check the driver installation: Make sure the board driver is installed correctly;
Check the cable connection: Check whether the USB cable or network cable is plugged in and not damaged;
Replace the cable and adapter board: If the cable is damaged or the adapter board is faulty, replace it in time.
No action after power on
- Problem description: The device does not move after power on, which may be caused by power failure, emergency stop switch pressed, control card or driver failure, etc.
- Solution: Check the power supply: Make sure the device is powered on and the air switch is not tripped;
Check the emergency stop switch: Make sure the emergency stop switch is not pressed;
Check the control card and driver: If the control card or driver fails, repair or replace it in time.
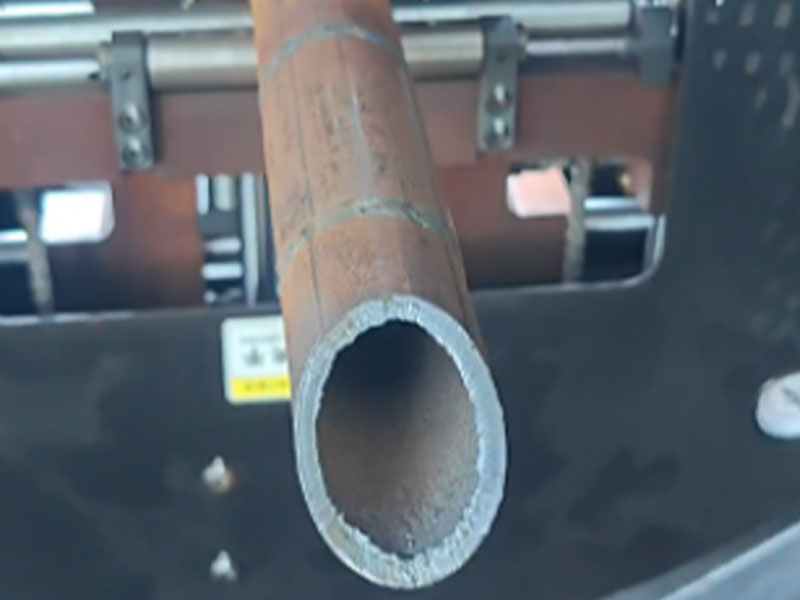
The machine stops engraving, misses engraving, or randomly engraves
- Problem description: The machine may stop engraving, miss engraving, or randomly engrave during the cutting process, which may be related to poor grounding, computer setting problems, original graphics errors, or control card failures.
- Solution: Check the ground wire: Make sure the ground wire is well grounded, and the resistance to ground should not be greater than 5 ohms;
Check the computer settings: Cancel the screen protection and power saving mode settings to ensure that the computer works stably;
Check the original graphics: Make sure the original graphics are correct, without crossover, unclosed or missing strokes; - Check the control card: If the control card fails, it needs to be repaired or replaced in time, or contact the laser cutting machine manufacturer in time.
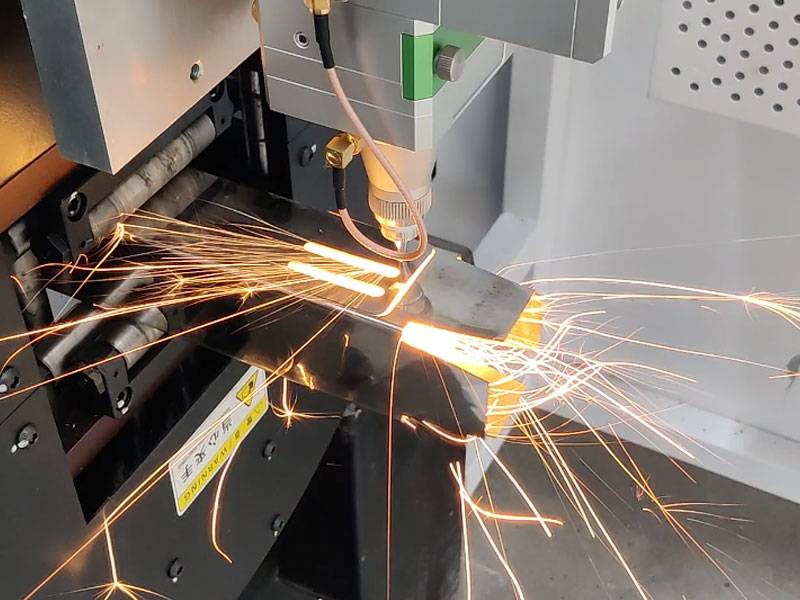
FAQ
What color laser is the strongest
The color of a laser doesn’t determine its strength. What actually determines a laser’s power is its output power, measured in watts (W) or milliwatts (mW).
Laser intensity can be measured in different ways – power output, perceived brightness, and ability to ignite materials. While blue lasers are technically the strongest in terms of power and intensity, green lasers may appear brighter and more noticeable in many applications.
Why are there burrs on the cut edge?
- Common causes: Cutting speed is too slow, auxiliary gas pressure is insufficient, focal point is offset.
- Solutions: Increase cutting speed appropriately, adjust auxiliary gas pressure, and calibrate the focal position.
Why is there an oxide layer on the cut surface?
- Common causes: Cutting speed is too slow, auxiliary gas flow is insufficient, material properties.
- Solutions: Increase cutting speed appropriately, increase auxiliary gas flow, and select appropriate cutting parameters.
Why is there a strange noise during cutting?
- Common causes: Mechanical parts are loose, guida rails are worn, cooling system malfunction.
- Solutions: Inspect and tighten mechanical parts, lubricate guida rails, and check the cooling system.
Why does the laser cutter often fail?
- Common causes: Unstable power supply, poor cooling water circulation, aging electronic components.
- Solutions: Stabilize the power supply, check the cooling water circulation system, and replace aging electronic components.