When it comes to H-beam fabrication, choosing the right laser cutting setup can significantly impact your productivity, cut quality, and overall project cost. Today’s market offers a variety of technologies—from fiber and CO2 lasers to plasma cutting alternatives—each with its own advantages and trade-offs. Key components such as the laser head, optics and lens coatings, as well as parameter adjustments, play a vital role in achieving precise, high-quality results.
This blog post will explore the key considerations for making an informed decision on the best H beam laser cutting machine setup for your operation.
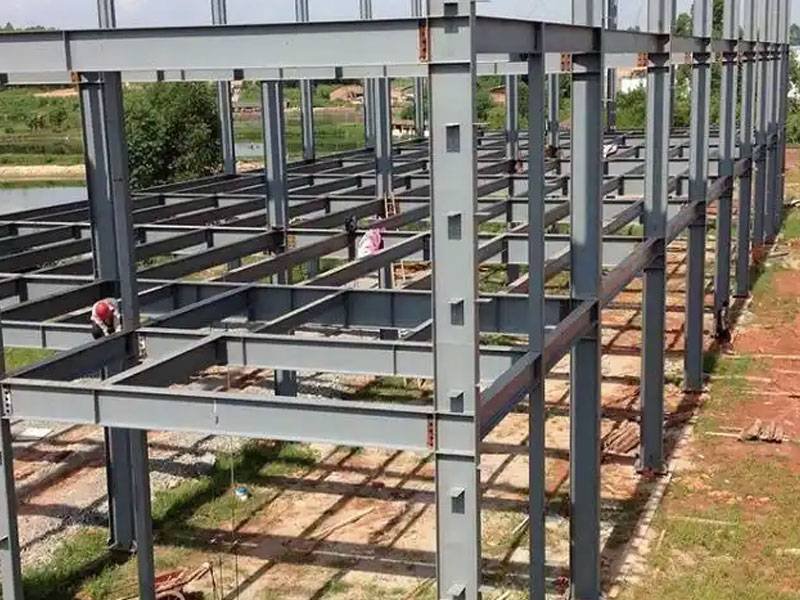
Comparison of Fiber and CO2 H Beam Laser Cutting Machine
Fiber and CO2 lasers each have their own unique advantages. Fiber lasers generally offer greater energy efficiency and faster cutting speeds, especially when cutting thin and medium-thick materials. They tend to have longer lifespans, lower maintenance requirements, and more stable beam delivery systems, making them an excellent choice for production lines where speed and consistency are important.
CO2 lasers have long been the backbone of the industry, providing exceptionally smooth cuts. While they may require more maintenance due to mirror and gas changes, they still excel when cutting thicker sections and can provide fine edge quality when properly adjusted.
H Beam Laser Cutting Machines vs. Plasma Cutters
- Plasma cutters can cut thicker steel quickly and cost-effectively, but their accuracy and edge quality generally lag behind what laser systems can achieve.
- H-type laser cutters offer tighter tolerances, minimal heat-affected zones, and cleaner edges.
- Plasma cutting is a concern in situations where initial equipment cost is a concern, but if your goal is high-precision manufacturing and reduced post-processing, laser systems are often a better choice.
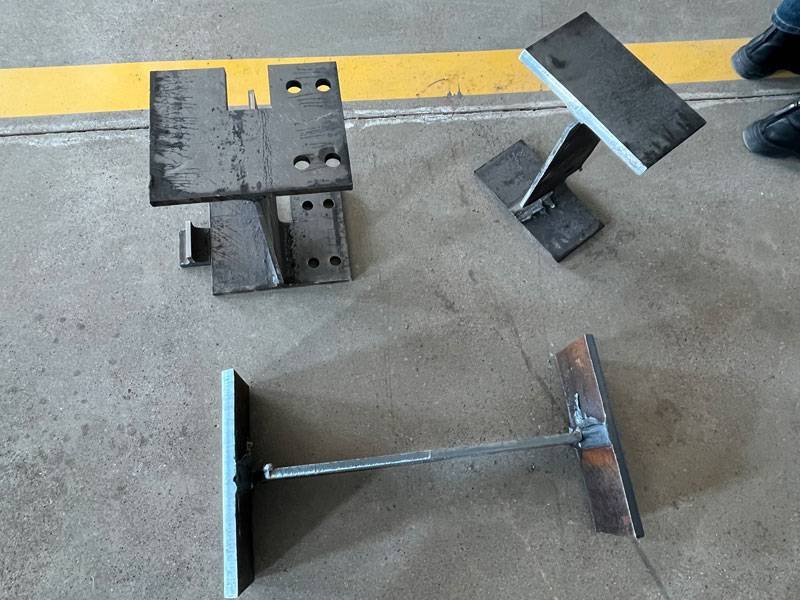
High-Power Fiber Lasers: Unlocking Enhanced H Beam Cutting Performance
High-power fiber lasers open up new frontiers for manufacturers seeking maximum throughput. Higher-wattage fiber lasers can process thicker materials more efficiently without sacrificing cut quality, enabling you to process a wider range of H-beam sizes and profiles. These powerful systems often integrate seamlessly with advanced CNC control and automation solutions, ensuring faster cycle times and reduced manual intervention.
Selecting Laser Heads and Optics for High-Precision H Beam Cutting
- The laser head and optics configuration is critical to achieving the level of precision required for structure manufacturing. Quality laser heads typically feature autofocus capabilities, powerful cooling systems, and specialized optics to maintain beam integrity.
- Optics, including lenses and mirrors, determine how well the laser beam is focused and delivered to the workpiece.
- The right combination can minimize beam distortion, improve edge quality, and achieve fine contours on complex shapes.
Entry-Level vs. High-End H Beam Laser Cutting Machines
Entry-level systems may have lower upfront costs, but may have limited functionality (cutting speed, thickness capabilities, automation features).
High-end machines offer better energy efficiency, greater power output, automatic loading/unloading options, and integration with advanced software solutions.
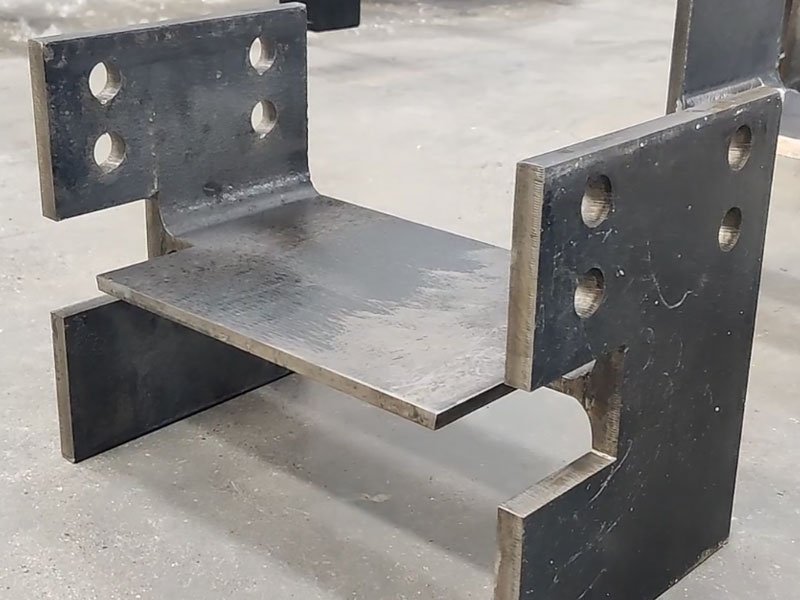
Adjusting Laser Cutting Parameters for Various H Beam Thicknesses
Cutting parameters (laser power, cutting speed, assist gas pressure and focus position) must be calibrated for different beam thicknesses and steel grades.
Thinner beams allow for faster cuts at lower power settings, while thicker sections require more power and slower feed rates to ensure smooth edges.
Proper parameter optimization minimizes material waste, reduces rework and ensures clean, consistent cuts.
Lens Coatings for Improved Cutting Clarity
Lens coatings significantly influence how the laser beam interacts with the workpiece. High-quality anti-reflective and protective coatings can improve beam transmission, reduce lens damage, and contribute to longer tool life. This attention to detail can yield clearer cuts, fewer defects, and less downtime for maintenance or lens replacement.
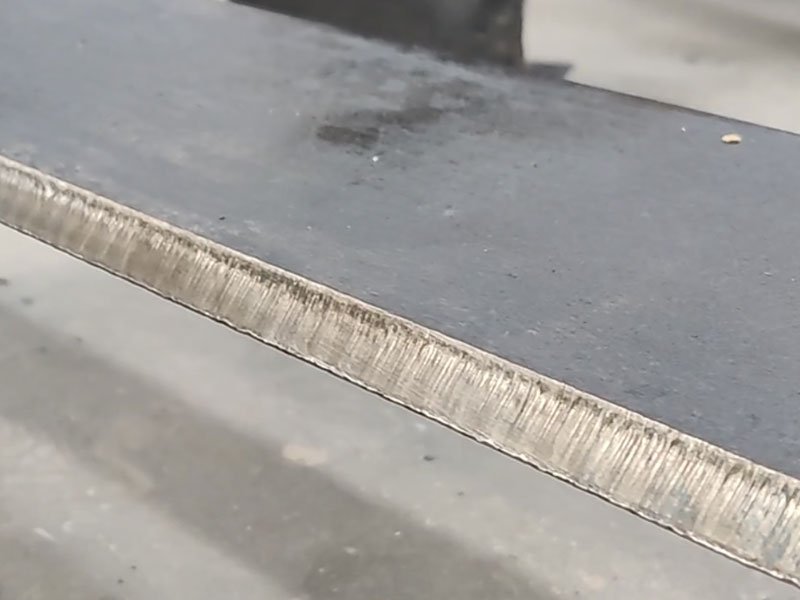
Conclusione
Choosing the right H-beam laser cutting setup requires balancing multiple factors—machine type, cutting technology, automation features, optical quality, and parameter fine-tuning. By understanding how fiber compares to CO2, lasers compare to plasma, and how the various components affect cut quality, you can make an informed decision that meets your production goals.