Precise specifications in tube laser cutting ensure optimal results. Accuracy minimizes material waste and enhances production efficiency. Planar tube laser cuts offer significant advantages. These include 49% more time efficiency y 31% cost efficiency per part. This method excels in creating complex designs with high precision. Manufacturers benefit from reduced production times and lower costs.
Understanding how to specify planar tube laser cut procedures is crucial for achieving these benefits.
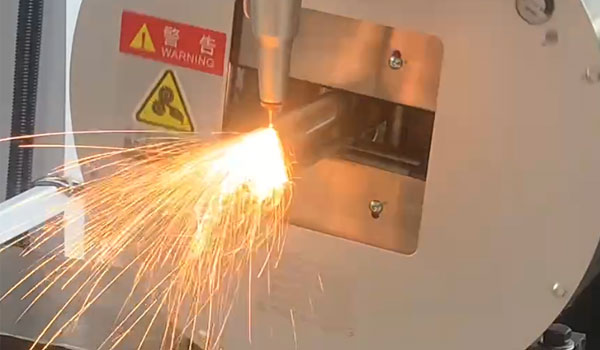
What is Planar Tube Laser Cutting
Planar tube laser cutting involves using a laser to cut tubes and profiles with high precision. This method utilizes advanced fiber laser technology to achieve clean and accurate cuts. The laser beam focuses on the material, melting or vaporizing it to create the desired shape. The process eliminates the need for multiple machining steps, enhancing efficiency.
What materials are Planar Tube Laser Cutting used for?
Planar tube laser cutting works with various materials
- Steel: Ideal for structural applications due to its strength.
- Aluminio: Preferred for lightweight and corrosion-resistant projects.
- Bahnbreite: 100–1250 mm: Suitable for food processing and medical devices because of its hygiene properties.
- Cobre: Used in electrical applications for its excellent conductivity.
Applications of Planar Tube Laser Cutting
Industries and Use Cases
- Automotor: Manufacturers use laser cutting for precise components and complex geometries.
- Construcción: Structural elements and frameworks often require laser-cut tubes.
- Muebles: Designers create intricate patterns and shapes with laser cutting.
- Dispositivos médicos: Precision and cleanliness make laser cutting ideal for medical tools and equipment.
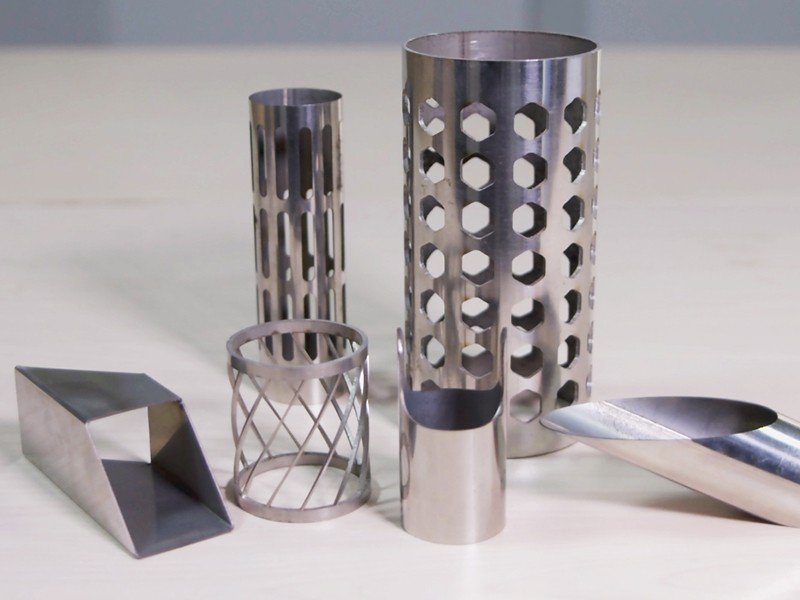
Advantages Over Traditional Cutting Methods
- Precisión: Laser cutting achieves higher accuracy than traditional methods.
- Velocidad: Faster cutting speeds reduce production times significantly.
- Flexibilidad: The ability to cut various materials and thicknesses enhances versatility.
- Cost Efficiency: Reduced material waste and lower labor costs result in overall savings.
Product Information:
- Tube Laser Cutting Machines handle various tube sizes and lengths with precision.
- Planar Fiber Laser Cutting Machines integrate advanced motion control systems and CNC controllers for seamless operation.
- Stealth Machine Tools provide speed and accuracy, eliminating the need for multiple processes.
How to Specify Planar Tube Laser Cut
Gathering Necessary Information
Material Specifications
Accurate material specifications play a crucial role in how to specify planar tube laser cut procedures. Each material type has unique properties that affect the cutting process. For steel, consider its strength and thickness. Aluminum requires attention to its lightweight and corrosion-resistant nature. Stainless steel demands hygiene properties for applications in food processing and medical devices. Copper’s excellent conductivity makes it ideal for electrical applications. Understanding these characteristics ensures optimal laser cutting results.
Design Requirements
Design requirements form the foundation of how to specify planar tube laser cut operations. Start by creating detailed design drawings. Include dimensions, angles, and tolerances. Use CAD software to develop precise models. Ensure that cutouts or designs are large enough for accurate laser cutting. Consider the complexity of the design and the material’s behavior during cutting. Properly defined design requirements lead to efficient and precise cuts.
Tools and Software Needed
CAD Software
CAD software is essential for how to specify planar tube laser cut processes. Programs like SolidWorks and AutoCAD allow for the creation of detailed 3D models. These models guía the laser cutter in executing precise cuts. CAD software helps in normalizing the cut, ensuring precision and accuracy. Advanced features in CAD software enable the simulation of the cutting process. This helps in identifying potential issues before actual cutting.
Laser Cutting Machines
Laser cutting machines are the backbone of how to specify planar tube laser cut tasks. These machines handle various tube sizes and lengths with high precision. Planar fiber laser cutting machines integrate advanced motion control systems and CNC controllers. This integration ensures seamless operation and superior cutting quality. Stealth machine tools provide speed and accuracy, eliminating the need for multiple processes. Selecting the right laser cutting machine based on material and design requirements is crucial for achieving optimal results.
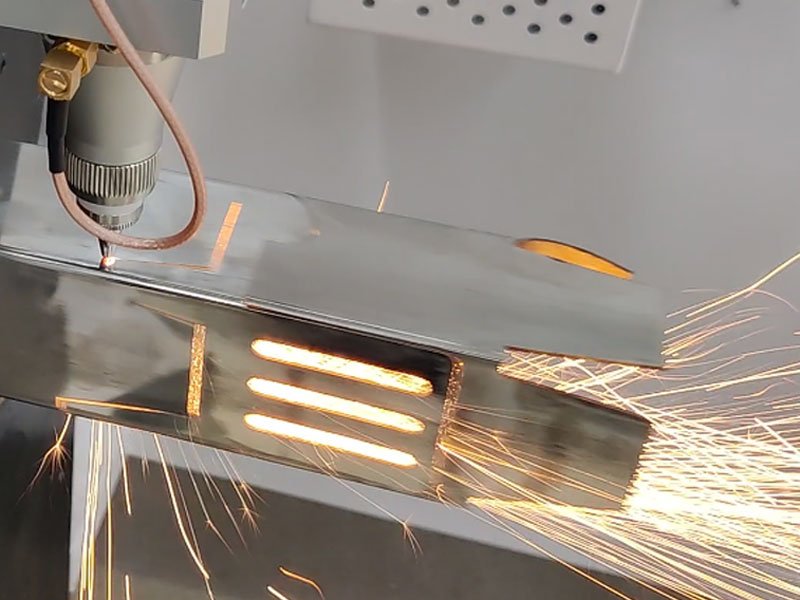
Sac Levha Nasıl Düz Kesilir: Kapsamlı Bir Kılavuz
Designing the Cut
Creating a CAD Model
Creating a CAD model forms the foundation of any laser cutting project. Use software like SolidWorks or AutoCAD to develop a detailed 3D representation of the tube. Include all necessary dimensions and angles. Ensure that the model accurately reflects the design requirements. The CAD model will guía the laser cutter in executing precise cuts.
Defining Cut Paths and Dimensions
Defining cut paths and dimensions is crucial for achieving accurate results. Specify the exact locations where the laser will cut. Include all necessary measurements, such as lengths and angles. Ensure that the cut paths align with the design specifications. Properly defined cut paths and dimensions will minimize errors during the cutting process.
Setting Up the Laser Cutter
Configuring Machine Settings
Configuring machine settings is essential for optimal performance. Adjust the laser power and speed based on the material being cut. Set the focus height to ensure a clean cut. Input the cut paths and dimensions from the CAD model into the machine’s control system. Proper configuration will enhance cutting accuracy and efficiency.
Loading the Material
Loading the material correctly ensures smooth operation. Place the tube securely on the machine’s worktable. Align the material according to the specified cut paths. Secure the tube to prevent movement during cutting. Proper loading will reduce the risk of misalignment and ensure precise cuts.
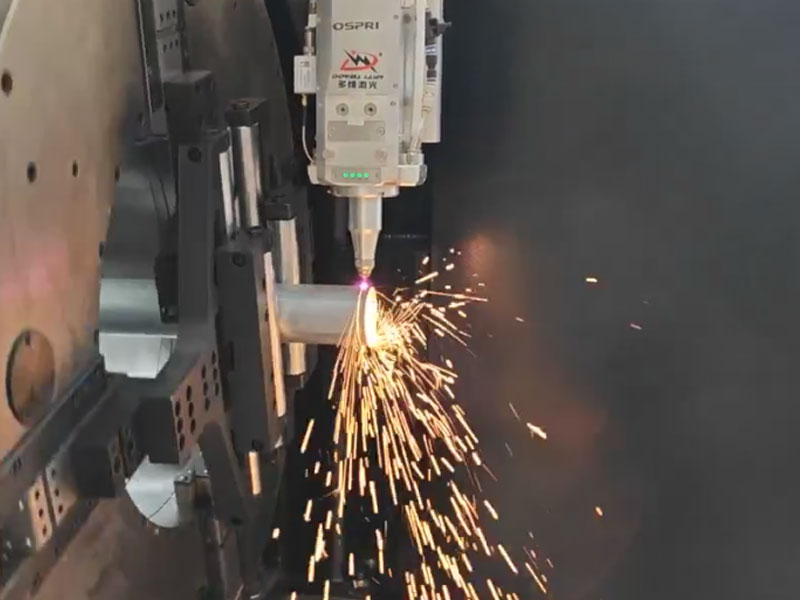
Executing the Cut
Running a Test Cut
Running a test cut helps identify potential issues before finalizing the project. Use a small section of the material to perform the test. Check the cut for accuracy and precision. Make any necessary adjustments to the machine settings or cut paths. A successful test cut will ensure that the final cut meets the design specifications.
Making Adjustments
Making adjustments based on the test cut results is crucial. Modify the laser power, speed, or focus height if needed. Adjust the cut paths to correct any misalignments. Ensure that all changes align with the design requirements. Proper adjustments will enhance the overall quality of the cut.
Finalizing the Cut
Finalizing the cut involves executing the full cutting process. Run the laser cutter according to the configured settings and defined cut paths. Monitor the process to ensure everything operates smoothly. Once the cut is complete, inspect the final product for accuracy and precision. A well-executed cut will meet all design specifications and quality standards.
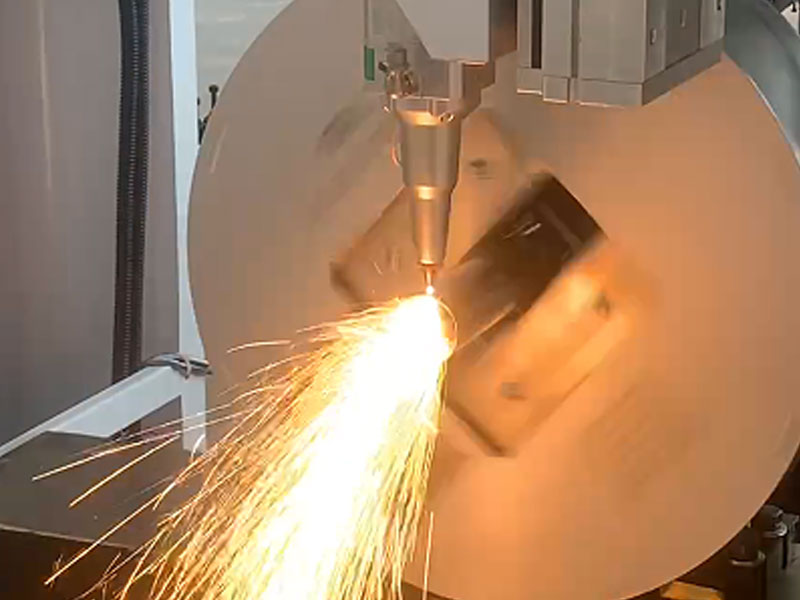
Quality Control and Troubleshooting
Inspecting the Cut
Checking for Precision and Accuracy
Inspecting the cut remains a crucial step in ensuring quality. Use calipers or micrometers to measure the dimensions of the cut. Compare these measurements with the design specifications. Any deviations can indicate issues with the cutting process.
Visual inspection also plays an important role. Look for clean edges and consistent kerf width. Smooth surfaces without burrs or roughness signify a precise cut.
Identifying Common Issues
Several common issues can arise during laser cutting. Burrs or rough edges often indicate incorrect laser power settings. Inconsistent kerf width suggests misalignment or improper focus height. Discoloration or burn marks might result from excessive heat or slow cutting speed.
Troubleshooting Common Problems
Misalignment
Misalignment can cause significant inaccuracies in the final product. Check the alignment of the material on the worktable. Ensure that the tube remains securely fastened to prevent movement. Verify that the laser head aligns correctly with the cut paths. Adjustments to the machine’s control system may be necessary to correct any misalignment.
Inconsistent Cuts
Inconsistent cuts often stem from variations in laser power or speed. Review the machine settings to ensure consistency. Adjust the laser power and speed based on the material’s properties. Conduct test cuts to verify the settings before proceeding with the final cut.
Surface quality can also affect cut consistency. Clean the material’s surface to remove any contaminants. Regular maintenance of the laser cutter, including lens cleaning and alignment checks, helps maintain consistent performance.
By following these steps, manufacturers can ensure high-quality planar tube laser cuts. Accurate inspections and effective troubleshooting lead to precise and reliable results.
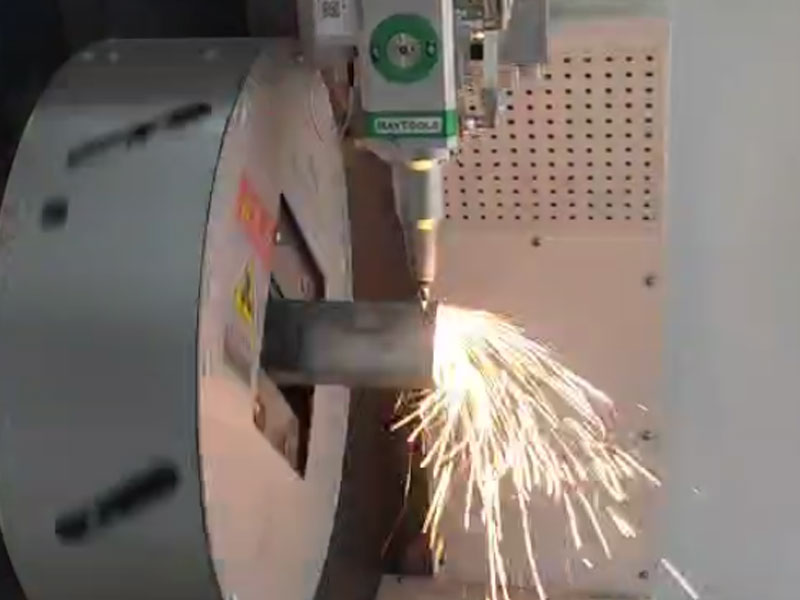
Precise specifications in tube laser cutting ensure optimal results. Accurate details minimize material waste and enhance production efficiency. Applying the outlined steps guarantees successful laser cutting. Manufacturers achieve high-quality cuts by following these guidelines.
Planar tube laser cuts offer significant benefits. These include time efficiency, cost savings, and superior precision. Advanced fiber laser technology enables complex designs with clean edges. Industries benefit from reduced production times and lower costs. Embracing planar tube laser cutting elevates manufacturing standards.